- Published: September 2015
- REF/ISBN: 9780852937310
- Edition: 1st
Publications in this series
Guidance on meeting expectations of EI process safety management framework
- Element 1: Leadership, commitment and responsibility
- Element 2: Identification and compliance with legislation and industry standards
- Element 3: Employee selection, placement and competency, and health assurance
- Element 4: Workforce involvement
- Element 5: Communication with stakeholders
- Element 6: Hazard identification and risk assessment
- Element 7: Documentation, records and knowledge management
- Element 8: Operating manuals and procedures
- Element 9: Process and operational status monitoring, and handover
- Element 10: Management of operational interfaces
- Element 11: Standards and practices
- Element 12: Management of change and project management
- Element 13: Operational readiness and process start-up
- Element 14: Emergency preparedness
- Element 15: Inspection and maintenance
- Element 16: Management of safety critical devices
- Element 17: Work control, permit to work and task risk management
- Element 18: Contractor and supplier, selection and management
- Element 19: Incident reporting and investigation
- Element 20: Audit, assurance, management review and intervention
Foreword
Process safety management (PSM) is vital to ensuring safe and continued operations in major accident hazard (MAH) organisations. However, PSM is a multifaceted process, and a number of high profile incidents since 2005 have suggested that without a holistic understanding of the various factors required for effective PSM it can be difficult and inefficient to ensure, and measure, performance.
In 2010 the Energy Institute (EI) published High level framework for process safety management (PSM framework), which aimed to define what PSM should involve. Divided into four focus areas (process safety leadership, risk identification and assessment, risk management, and review and improvement) and sub-divided into 20 'elements', it sets out a framework of activities MAH organisations should undertake to ensure PSM. Each element lists a number of high level activities organisations should meet (expectations).
EI Guidance on meeting expectations of EI Process safety management framework is a series of 20 publications ('guidelines') that build on the PSM framework. Commissioned by the EI Process Safety Committee (PSC) each guideline captures and presents current industry good practices and guidance on how organisations can meet the expectations set out in each element of the PSM framework. Each guideline includes:
- a logical flow diagram of activities (steps) the organisation should undertake to manage that element;
- descriptions of those steps;
- example performance measures (PMs) to measure the extent to which key steps have been undertaken;
- a list of further resources to help undertake key steps;
- a table mapping the steps against the expectations in the PSM framework, and − annexes of useful information.
Readers implementing the guidance in this publication should be aware of the PSM framework and the other publications in this series, particularly if they are a manager with oversight of the wider implementation of PSM.
The information contained in this publication is provided for general information purposes only. Whilst the Energy Institute and the contributors have applied reasonable care in developing this publication, no representations or warranties, express or implied, are made by the Energy Institute or any of the contributors concerning the applicability, suitability, accuracy or completeness of the information contained herein and the Energy Institute and the contributors accept no responsibility whatsoever for the use of this information. Neither the Energy Institute nor any of the contributors shall be liable in any way for any liability, loss, cost or damage incurred as a result of the receipt or use of the information contained herein.
Suggested revisions are invited and should be submitted through the Technical Department, Energy Institute, 61 New Cavendish Street, London, W1G 7AR. e: [email protected]
1. Introduction
1.1 Management of change and project management
This guideline sets out good practices for management of health, safety and environment (HS&E) and process safety risks introduced into the business by project and non-project changes, ensuring that:
- all changes, large, small, permanent and temporary are systematically identified and assessed;
- identified HS&E risks are appropriately managed throughout the life of the change;
- all changes are reviewed and approved, by designated competent personnel, before they are implemented, and
- appropriate systems are in place to monitor and audit the management of change (MoC) process.
The introduction of any form of change into an organisation, if not appropriately managed, can significantly increase the levels of HS&E and process safety risk. Management should ensure that risks arising from any form of change are systematically identified, assessed and managed.
1.2 Expectations for element 12: Management of change and project management
Element 12 of EI High level framework for process safety management ('PSM framework') describes 17 expectations – arrangements and processes that organisations should (to an appropriate degree) have in place in order to ensure they are managing this aspect of process safety management (PSM) appropriately:
'Overview | The introduction of any form of change into an organisation, if not appropriately managed, can significantly increase the levels of HS&E and process safety risk. Management must ensure that risks arising from any form of change are systematically identified, assessed and managed. |
12.1 | A process is in place which systematically identifies, assesses and manages the risks arising from both temporary and permanent changes. |
12.2 | The processes for managing change address: − authority for approval of changes; − compliance with legislation and approved standards; − acquisition of needed permits; − documentation, including reason and technical basis for change; − communication of risks associated with the change, and − mitigation measures, such as: time limitation; training. |
12.3 | Management of change addresses changes to: − assets or equipment; − operations or operating procedures; − products, materials or substances; − organisation or personnel; − software or control systems; − designs or specifications; − standards or practices, and − inspection, maintenance or testing programmes. |
12.4 | Management of change considers impacts to: − health and safety (including process safety); − environment; − reputation; − security; − third party assets, and − business interruption. |
12.5 | Management of change considers human and organisational factors. |
12.6 | Temporary changes do not exceed initial authorisation for scope or time without review and approval. |
12.7 | Changes are approved by specified named competent individuals commensurate with the risk associated with the proposed change. |
12.8 | Pertinent records covering all changes are maintained. |
12.9 | Project management procedures are documented, well understood, readily available to those who need to use them (including contractors) and executed by qualified personnel. |
12.10 | Key stages in the project development life cycle are reviewed and approved by specified level of management with due consideration of PSM practices. |
12.11 | Criteria are established and procedures are in place for conducting and documenting risk assessments at specific project stages to confirm the integrity of new assets and existing assets which have been substantially modified. |
12.12 | HS&E and process safety impacts of new business development on the local community are assessed and communicated to relevant authorities and integrated into the business case. |
12.13 | The design and construction of new or modified facilities use approved standards and practices that: − meet or exceed applicable regulatory requirements; − embody responsible requirements where legislation does not exist, and − encompass robust PSM practices. |
12.14 | A pre-commissioning review is performed and documented to confirm that: − construction is in accordance with specifications; − EI PSM framework measures are in place; − risk management recommendations have been addressed and required actions taken; − regulatory and permit requirements are met; − emergency, operations and maintenance procedures are in place and adequate; − required training of personnel and communication related to PSM aspects have been accomplished, and − necessary project documentation (safety file) is readily available to those who need to use it. |
12.15 | Procedures are in place to identify and manage the HS&E and process safety risks arising from the mothballing and decommissioning or disposal of assets including dismantling, demolition and site remediation. |
12.16 | Arrangements for management of change and project management are understood and followed; understanding of arrangements and compliance with them is regularly tested. |
12.17 | Compliance and performance trends are reviewed by specified levels of management.' |
This guideline provides a process, along with guidance, to help organisations meet these expectations. It also suggests a number of compliance checks and performance measures (PMs) to measure the extent to which key activities involved in meeting these expectations have been or are being undertaken.
2. Arrangements for meeting expectations
Figure 1 provides a logical flow diagram for the activities that should be in place to meet the expectations in element 12, regarding MoC and project management. It covers activities (steps) which should be undertaken by the organisation, across three phases: set-up (preparations to manage the element); operate (management of the element); and monitor, review and intervene (monitoring and reviewing the management of the element, and making appropriate interventions if the element is not being managed effectively). Figure 2 provides separate operational processes for project management.
The flow diagram provides an example of the logical arrangement of necessary activities. The reader should take cues from the arrangement and relationships between steps when determining the appropriate flow design for their own organisation. The flow diagram also shows interfaces with other elements, where this element may be dependent upon activities that are addressed by other elements – e.g. step 2 relies on there being an effective competence management system in place, as described in Guidance on meeting expectations of EI Process safety management framework Element 3: Employee selection, placement and competency, and health assurance.
At specific points in the flow diagram process, PMs are suggested. These PMs are predominantly leading indicators designed to enable the measurement of the outputs from the element and the level of operational compliance with the expectations. Suggested PMs are described further in section 3.
2.1 provides guidance on the actions involved for each step, the deliverables that should result from those actions, and the frequency at which the step should be undertaken. It also provides more detailed guidance notes.
provides more detailed guidance notes. These steps have been mapped against element 12 expectations in Annex C. Note that some expectations are fulfilled through several steps, and some steps help fulfil several expectations; however, all steps should be undertaken. As such, Annex C is for reference purposes only, to demonstrate that the arrangements outlined in this guideline enable the organisation to work towards fulfilling the requirements set out in element 12 of the PSM framework.
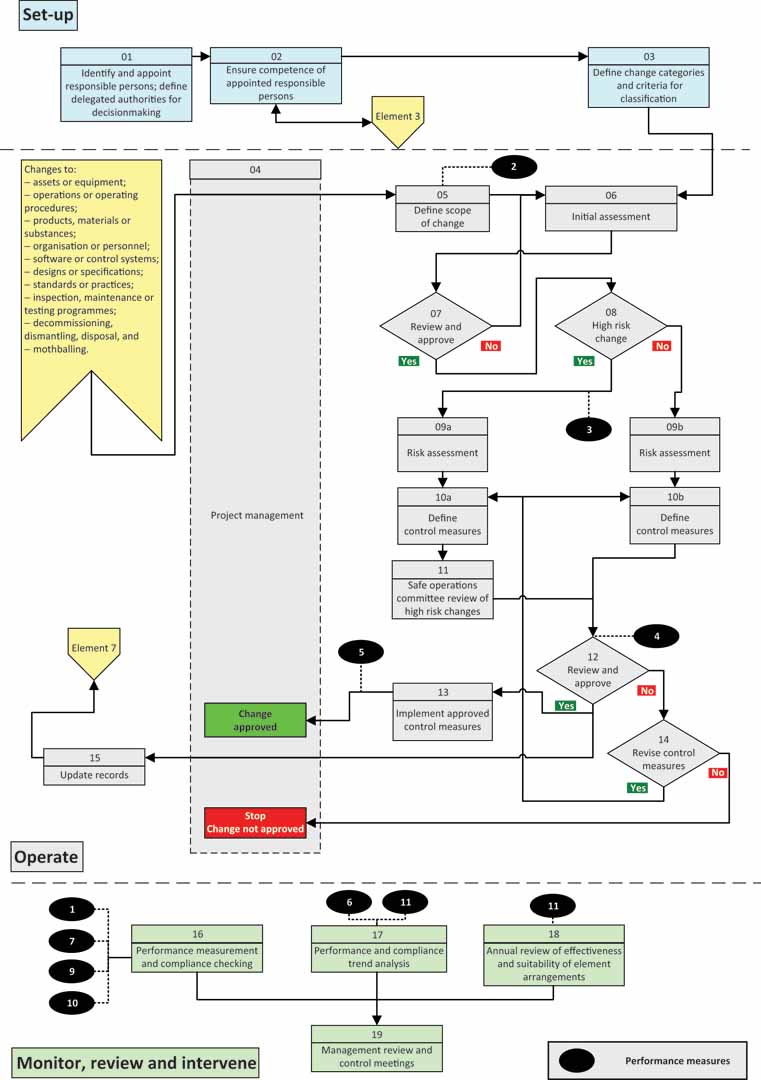
Figure 1: Logical flow diagram
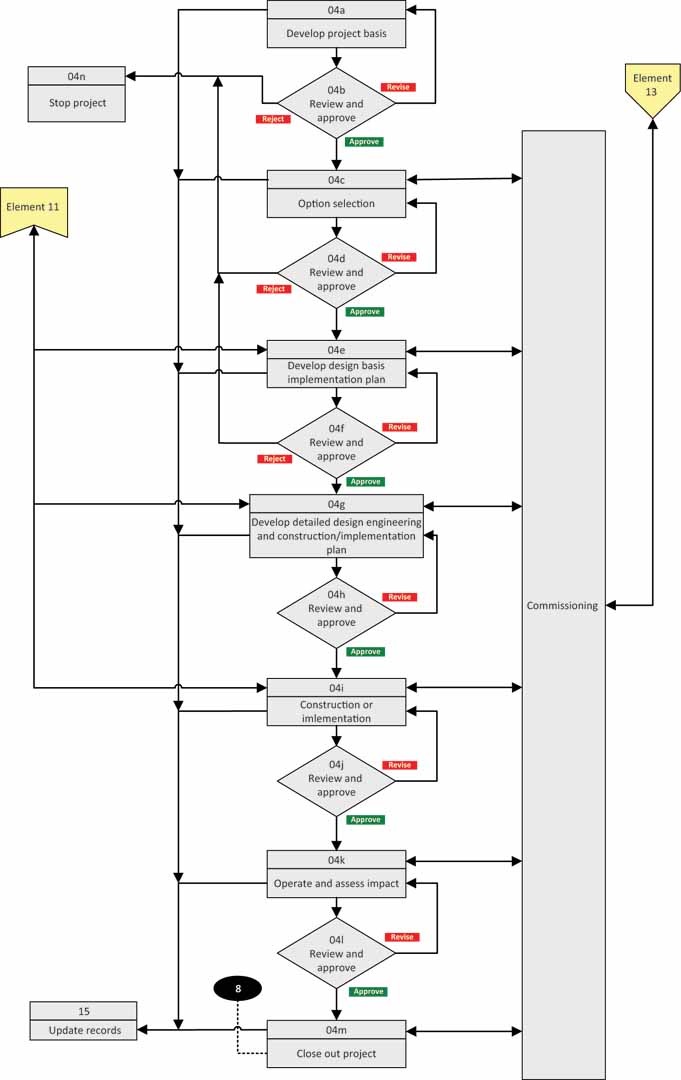
Figure 2: Step 4 expanded
2.1 Descriptions of actions for each step in the logical flow diagram
Actions
Identify and appoint responsible persons; define delegated authorities for decision making
Identify and appoint persons who will have defined roles and responsibilities for each aspect of the arrangements for leadership, commitment and responsibility.
Deliverables
Defined roles and responsibilities.
Agreed list of responsible persons who will:
- act as element owner, and
- carry out each aspect of the arrangements for the element.
Defined delegated authorities for decision making.
Agreed list of delegated authorities for each identified responsible person/position.
Frequency
During implementation; then as required.
Guidance notes:
The senior accountable person, typically a director, business unit (BU) leader or site manager should ensure that accountabilities and responsibilities are assigned for each step in the process. Typically, this can be achieved by appointing an element owner who will work with line managers to agree and assign these accountabilities and responsibilities.
Typically, the element owner should be a senior line manager.
During the implementation phase the element owner should coordinate the implementation of the element across the organisation, BU or site on behalf of the senior accountable person, working with other senior line managers to ensure that the implementation is appropriately planned and resourced and that any issues are resolved.
The element owner should also ensure that delegated authorities for decision making within the element are defined and approved.
Following implementation, during the operational phase the element owner should work with the other senior line managers to ensure that the element continues to operate as intended. In effect the element owner should act as a coach to the management team, building their understanding and confidence in the use of the element.
Actions
Ensure competence of appointed responsible persons
Deliverables
Training material.
Competency assessment.
Training schedule.
Competent persons.
Frequency
During implementation; then as required.
Guidance notes:
The element owner should ensure that the required competencies are defined and agreed for all persons with assigned roles and responsibilities within the element, and that each of these people is trained and coached appropriately to develop these required competencies.
They should also ensure that training and development programmes and routine personnel performance appraisals take into account these required competencies. This should be accomplished by means of Guidance on meeting expectations of EI Process safety management framework Element 3: Employee selection, placement and competency, and health assurance.
Actions
Define change categories and criteria for classification
Define change categories and criteria for classification as either high risk or low risk changes.
Deliverables
Agreed list of change categories.
Approved criteria for classification of changes as either high risk or low risk.
Frequency
During implementation; then updated as required (review annually).
Guidance notes:
The organisation should define clear categories for the different types of change which the organisation may expect to see, and for each one identify the approach to risk identification and assessment which should be adopted for each different type of change. The approach to risk identification and assessment should address risks to:
- health and safety (including process safety);
- environment;
- reputation;
- security;
- third party assets, and
- business continuity.
The change categories should include:
- assets or equipment;
- operations or operating procedures;
- products, materials or substances;
- organisation or personnel;
- software or control systems;
- designs or specifications;
- standards or practices;
- inspection, maintenance or testing programmes;
- decommissioning, dismantling, disposal, and
- mothballing.
It is also helpful to define the criteria for differentiating between high and low risk changes, together with the risk assessment approach and review arrangements which should be adopted for each of these classifications.
During the implementation phase the element owner should ensure that these are clearly defined and ensure that they are incorporated into the training and competency assurance for the personnel who will be expected to make use of the MoC and project management arrangements.
These categories and criteria should be reviewed and approved by personnel with the delegated authority to do so.
Actions
Develop project basis
Deliverables
Agreed project basis:
- identified issue or opportunity;
- incentives to progress;
- identified options to address issue or capture opportunity;
- outline project implementation plan, and
- appropriate class of cost estimate and schedule.
Completed risk assessment.
Decision to progress or stop.
Identified 'technical queries'.
Issues to be addressed in the next phase.
Frequency
As required by the schedule.
Guidance notes:
Discretionary expenditure on 'capital' or 'expense' projects is typically used to either remove unacceptable risk (HS&E, reputation, business interruption, financial) or to capture opportunities (justified and affordable return on investment). Developing the portfolio of capital and expense projects which need to be progressed within a budget period (budget development) can be quite challenging. A suggested approach to this is shown in Annex J.
The project basis should address the issue which needs to be solved or the opportunity to be captured. At this stage the primary focus should be on the incentives and justification for addressing the issue or capturing the opportunity.
The project basis should identify a range of options to address the issue or capture the opportunity; selection of the most suitable option is carried out in the next stage.
At this initial stage of the project development it should be considered how the project will be developed, and what skills and competencies will be required for each stage of the development and implementation, and whether they will be available when required. This, together with the initial schedule, forms the outline implementation plan. An example is shown in Annex I.
The project basis should incorporate an initial assessment of the risks arising from the development and implementation of the proposed project, in accordance with the MoC risk assessment guidelines as defined in steps 5 – 15. Provision for the implementation of the identified control measures should be included in the project basis, and the cost estimated.
The development of the project basis should involve representatives of the project owner group who will take on the completed project and operate it, incorporating it into 'business as usual'. They should ensure that operability, maintainability and provision for commissioning are taken into account in the project basis in accordance with Guidance on meeting expectations of EI Process safety framework Element 13: Operational readiness and process start-up.
Technical queries raised by the owner group should be documented and closed out in a timely fashion. The development of the project basis should identify:
- the issue or opportunity to be addressed;
- identified options to address the issue or capture the opportunity;
- cost estimate of the appropriate class (accuracy and confidence level) and outline schedule;
- the incentives to progress the project;
- the outline project implementation plan;
- operability, maintainability and commissioning considerations;
- initial change risk assessment, and
- decision to progress or stop.
The completed project basis should be reviewed and approved by the appropriate line manager with the necessary competency and delegated level of authority.
Actions
Review and approve
Project basis reviewed and approved by the delegated authority.
Deliverables
Agreed project basis:
- identified issue or opportunity;
- incentives to progress;
- identified options to address issue or capture opportunity;
- outline project implementation plan, and
- appropriate class of cost estimate and schedule.
Completed risk assessment.
Decision to progress or stop.
Identified 'technical queries'.
Issues to be addressed in the next phase.
Frequency
As required by the schedule.
Guidance notes:
Discretionary expenditure on 'capital' or 'expense' projects is typically used to either remove unacceptable risk (HS&E, reputation, business interruption, financial) or to capture opportunities (justified and affordable return on investment). Developing the portfolio of capital and expense projects which need to be progressed within a budget period (budget development) can be quite challenging. A suggested approach to this is shown in Annex J.
The project basis should address the issue which needs to be solved or the opportunity to be captured. At this stage the primary focus should be on the incentives and justification for addressing the issue or capturing the opportunity.
The project basis should identify a range of options to address the issue or capture the opportunity; selection of the most suitable option is carried out in the next stage.
At this initial stage of the project development it should be considered how the project will be developed, and what skills and competencies will be required for each stage of the development and implementation, and whether they will be available when required. This, together with the initial schedule, forms the outline implementation plan. An example is shown in Annex I.
The project basis should incorporate an initial assessment of the risks arising from the development and implementation of the proposed project, in accordance with the MoC risk assessment guidelines as defined in steps 5 – 15. Provision for the implementation of the identified control measures should be included in the project basis, and the cost estimated.
The development of the project basis should involve representatives of the project owner group who will take on the completed project and operate it, incorporating it into 'business as usual'. They should ensure that operability, maintainability and provision for commissioning are taken into account in the project basis in accordance with Guidance on meeting expectations of EI Process safety framework Element 13: Operational readiness and process start-up.
Technical queries raised by the owner group should be documented and closed out in a timely fashion. The development of the project basis should identify:
- the issue or opportunity to be addressed;
- identified options to address the issue or capture the opportunity;
- cost estimate of the appropriate class (accuracy and confidence level) and outline schedule;
- the incentives to progress the project;
- the outline project implementation plan;
- operability, maintainability and commissioning considerations;
- initial change risk assessment, and
- decision to progress or stop.
The completed project basis should be reviewed and approved by the appropriate line manager with the necessary competency and delegated level of authority.
Actions
Option selection
Deliverables
Agreed option selection:
- selected option to address issue or capture opportunity;
- appropriate class of cost estimate and schedule;
- justification for selected option;
- incentives to progress, and
- updated outline project implementation plan.
Completed risk assessment.
Decision to progress or stop.
Identified technical queries.
Issues to be addressed in the next phase.
Frequency
As required by the schedule.
Guidance notes:
Following on from the approval of the project basis, the option selection should evaluate each of the identified options for addressing the issue or capturing the opportunity, and propose the most suitable for review and approval by the appropriate line manager with the necessary competency and delegated level of authority.
The development of the option selection should involve representatives of the owner group. They should ensure that operability, maintainability and commissioning are taken into account in the option selection in accordance with Guidance on meeting expectations of EI Process safety framework Element 13: Operational readiness and process start-up.
Technical queries raised by the owner group should be documented and closed out in a timely fashion.
The option selection should incorporate an initial assessment of the risks arising from the development and implementation of the proposed project, in accordance with the MoC risk assessment guidelines as defined in steps 5 – 15. Provision for the implementation of the identified control measures should be included in the option selection, and the cost estimated.
The development of the option selection should identify:
- the selected option to address the issue or capture the opportunity;
- the justification for the selected option;
- cost estimate of the appropriate class (accuracy and confidence level) and outline schedule;
- updated assessment of the incentives to progress the project;
- operability, maintainability and commissioning considerations;
- change risk assessment for the proposed option;
- updated outline project implementation plan, and
- decision to progress or stop.
Actions
Review and approve
Option reviewed and approved by the delegated authority.
Deliverables
Agreed option selection:
- selected option to address issue or capture opportunity;
- appropriate class of cost estimate and schedule;
- justification for selected option;
- incentives to progress, and
- updated outline project implementation plan.
Completed risk assessment.
Decision to progress or stop.
Identified technical queries.
Issues to be addressed in the next phase.
Frequency
As required by the schedule.
Guidance notes:
Following on from the approval of the project basis, the option selection should evaluate each of the identified options for addressing the issue or capturing the opportunity, and propose the most suitable for review and approval by the appropriate line manager with the necessary competency and delegated level of authority.
The development of the option selection should involve representatives of the owner group. They should ensure that operability, maintainability and commissioning are taken into account in the option selection in accordance with Guidance on meeting expectations of EI Process safety framework Element 13: Operational readiness and process start-up.
Technical queries raised by the owner group should be documented and closed out in a timely fashion.
The option selection should incorporate an initial assessment of the risks arising from the development and implementation of the proposed project, in accordance with the MoC risk assessment guidelines as defined in steps 5 – 15. Provision for the implementation of the identified control measures should be included in the option selection, and the cost estimated.
The development of the option selection should identify:
- the selected option to address the issue or capture the opportunity;
- the justification for the selected option;
- cost estimate of the appropriate class (accuracy and confidence level) and outline schedule;
- updated assessment of the incentives to progress the project;
- operability, maintainability and commissioning considerations;
- change risk assessment for the proposed option;
- updated outline project implementation plan, and
- decision to progress or stop.
Actions
Develop design basis and implementation plan
Deliverables
Agreed investment case, design basis and implementation plan:
- design basis for selected option;
- appropriate class of cost estimate and schedule;
- incentives to progress;
- implementation plan for selected option, and
- applicable design standards and construction practices.
Completed risk assessment.
Decision to progress or stop.
Identified technical queries.
Issues to be addressed in the next phase.
Frequency
As required by the schedule.
Guidance notes:
Following the approval of the option selection, the design basis and implementation plan should set out:
- for construction projects:
- The requirements and constraints which should be addressed in the detailed engineering, such as required throughputs, product qualities, available utilities and available plot area.
- for non-construction projects:
- The required deliverables which should be addressed by the detailed implementation plan and the constraints which should be taken into consideration.
The design basis should identify applicable design standards which should be applied to the detailed design engineering and the construction practices which should be incorporated into the construction plan.
The development of the design basis and implementation plan should involve representatives of the owner group. They should ensure that operability, maintainability and commissioning are taken into account in the design basis and implementation plan in accordance with Guidance on meeting expectations of EI Process safety framework Element 13: Operational readiness and process start-up.
Technical queries raised by the owner group should be documented and closed out in a timely fashion.
The design basis and implementation plan should include a review and update of the risk assessment developed for the option selection, taking into account the increased level of detail which is available. This risk assessment should be in accordance with the MoC risk assessment guidelines as defined in steps 5 – 15. Provision for the implementation of the identified control measures should be included in the design basis and implementation plan, and the cost estimated.
The development of the design basis and implementation plan should identify:
- design basis for selected option to address the issue or capture the opportunity;
- applicable design standards and construction practices;
- cost estimate of the appropriate class (accuracy and confidence level) and outline schedule;
- updated assessment of the incentives to progress the project;
- operability, maintainability and commissioning considerations;
- updated change risk assessment for the proposed option;
- implementation plan for the selected option, and
- decision to progress or stop.
The completed design basis and implementation plan should be reviewed and approved by an appropriate line manager with the necessary competency and delegated level of authority.
Actions
Review and approve
Design basis and implementation plan reviewed and approved by the delegated authority.
Deliverables
Agreed investment case, design basis and implementation plan:
- design basis for selected option;
- appropriate class of cost estimate and schedule;
- incentives to progress;
- implementation plan for selected option, and
- applicable design standards and construction practices.
Completed risk assessment.
Decision to progress or stop.
Identified technical queries.
Issues to be addressed in the next phase.
Frequency
As required by the schedule.
Guidance notes:
Following the approval of the option selection, the design basis and implementation plan should set out:
- for construction projects:
- The requirements and constraints which should be addressed in the detailed engineering, such as required throughputs, product qualities, available utilities and available plot area.
- for non-construction projects:
- The required deliverables which should be addressed by the detailed implementation plan and the constraints which should be taken into consideration.
The design basis should identify applicable design standards which should be applied to the detailed design engineering and the construction practices which should be incorporated into the construction plan.
The development of the design basis and implementation plan should involve representatives of the owner group. They should ensure that operability, maintainability and commissioning are taken into account in the design basis and implementation plan in accordance with Guidance on meeting expectations of EI Process safety framework Element 13: Operational readiness and process start-up.
Technical queries raised by the owner group should be documented and closed out in a timely fashion.
The design basis and implementation plan should include a review and update of the risk assessment developed for the option selection, taking into account the increased level of detail which is available. This risk assessment should be in accordance with the MoC risk assessment guidelines as defined in steps 5 – 15. Provision for the implementation of the identified control measures should be included in the design basis and implementation plan, and the cost estimated.
The development of the design basis and implementation plan should identify:
- design basis for selected option to address the issue or capture the opportunity;
- applicable design standards and construction practices;
- cost estimate of the appropriate class (accuracy and confidence level) and outline schedule;
- updated assessment of the incentives to progress the project;
- operability, maintainability and commissioning considerations;
- updated change risk assessment for the proposed option;
- implementation plan for the selected option, and
- decision to progress or stop.
The completed design basis and implementation plan should be reviewed and approved by an appropriate line manager with the necessary competency and delegated level of authority.
Actions
Develop detailed design engineering and construction/ implementation plan
Deliverables
Approved detailed design engineering (for construction projects):
- design meets applicable design standards, and
- identified design follow-up requirements.
Approved detailed construction or implementation plan and schedule:
- incorporating required construction practices;
- identified constructability or implementation issues;
- identified commissioning issues;
- identified technical queries, and
- issues to be addressed in the next phase.
Completed risk assessment.
Frequency
As required by the schedule.
Guidance notes:
Following on from the approval of the design basis and implementation plan, the detailed design engineering and construction/detailed implementation plan should set out:
- detailed design engineering (for construction projects) approved for construction, and
- approved detailed construction or implementation plan and schedule:
- incorporating required construction practices;
- identified constructability or implementation issues, and
- identified commissioning issues.
The development of the detailed design engineering and construction/implementation plan should involve representatives of the owner group. They should ensure that operability, maintainability and commissioning are taken into account in the detailed design engineering and construction/implementation plan in accordance with Guidance on meeting expectations of EI Process safety framework Element 13: Operational readiness and process start-up.
Technical queries raised by the owner group should be documented and closed out in a timely fashion.
The detailed design engineering and construction/implementation plan should include a review and update of the risk assessment developed for the design basis, taking into account the increased level of detail which is available. This risk assessment should be in accordance with the MoC risk assessment guidelines as defined in steps 5 – 15.
Provision for the implementation of the identified control measures should be included in the detailed design engineering and construction/implementation plan, and the cost estimated.
The development of the detailed design engineering and construction/implementation plan should identify:
- approved detailed design engineering (for construction projects):
- design meets applicable design standards, and
- identified design follow-up requirements.
- approved deviations from applicable design standards, together with associated required control measures;
- approved detailed construction or implementation plan and schedule; incorporating required construction practices;
- identified constructability or implementation issues;
- identified operability, maintainability and commissioning considerations;
- updated change risk assessment;
- updated cost estimate of the appropriate class (accuracy and confidence level) and outline schedule;
- updated assessment of the incentives to progress the project, and
- decision to progress or stop.
The completed detailed design engineering and construction/implementation plan should be reviewed and approved by appropriate nominated personnel with the necessary competency and delegated level of authority.
Actions
Review and approve
Detailed design engineering and construction/ implementation plan reviewed and approved by the delegated authority
Deliverables
Approved detailed design engineering (for construction projects):
- design meets applicable design standards, and
- identified design follow-up requirements.
Approved detailed construction or implementation plan and schedule:
- incorporating required construction practices;
- identified constructability or implementation issues;
- identified commissioning issues;
- identified technical queries, and
- issues to be addressed in the next phase.
Completed risk assessment.
Frequency
As required by the schedule.
Guidance notes:
Following on from the approval of the design basis and implementation plan, the detailed design engineering and construction/detailed implementation plan should set out:
- detailed design engineering (for construction projects) approved for construction, and
- approved detailed construction or implementation plan and schedule:
- incorporating required construction practices;
- identified constructability or implementation issues, and
- identified commissioning issues.
The development of the detailed design engineering and construction/implementation plan should involve representatives of the owner group. They should ensure that operability, maintainability and commissioning are taken into account in the detailed design engineering and construction/implementation plan in accordance with Guidance on meeting expectations of EI Process safety framework Element 13: Operational readiness and process start-up.
Technical queries raised by the owner group should be documented and closed out in a timely fashion.
The detailed design engineering and construction/implementation plan should include a review and update of the risk assessment developed for the design basis, taking into account the increased level of detail which is available. This risk assessment should be in accordance with the MoC risk assessment guidelines as defined in steps 5 – 15.
Provision for the implementation of the identified control measures should be included in the detailed design engineering and construction/implementation plan, and the cost estimated.
The development of the detailed design engineering and construction/implementation plan should identify:
- approved detailed design engineering (for construction projects):
- design meets applicable design standards, and
- identified design follow-up requirements.
- approved deviations from applicable design standards, together with associated required control measures;
- approved detailed construction or implementation plan and schedule; incorporating required construction practices;
- identified constructability or implementation issues;
- identified operability, maintainability and commissioning considerations;
- updated change risk assessment;
- updated cost estimate of the appropriate class (accuracy and confidence level) and outline schedule;
- updated assessment of the incentives to progress the project, and
- decision to progress or stop.
The completed detailed design engineering and construction/implementation plan should be reviewed and approved by appropriate nominated personnel with the necessary competency and delegated level of authority.
Actions
Construction or implementation
Deliverables
Construction projects completed:
- to meet detailed design engineering;
- to meet required construction practices;
- to cost, and
- to schedule.
Non-construction projects completed:
- to meet detailed implementation plan;
- to cost, and
- to schedule.
Project handed over to owner who is ready, willing and able to accept and operate it.
Agreed items to be addressed post start-up.
Frequency
As required by the schedule.
Guidance notes:
The construction or implementation should:
- for construction projects, be completed:
- to meet detailed design engineering;
- to meet required construction practices;
- to cost, and
- to schedule.
- for non-construction projects be completed:
- to meet detailed design implementation plan;
- to cost, and
- to schedule.
The project should be handed over to an owner who is ready, willing and competent to operate it. The handover should include a list of agreed outstanding items which will be addressed post start-up.
Throughout the construction/implementation any changes to the approved detailed design engineering and detailed implementation plan should be subjected to thorough assessment of the risks arising from these changes, in accordance with the MoC risk assessment guidelines as defined in steps 5 – 15.
All changes to the approved detailed design engineering and detailed implementation plan should be approved by appropriate nominated personnel with the necessary competency and delegated level of authority.
When the construction/implementation is completed, the completion status should be formally reviewed and accepted by the appropriate line manager with the necessary competency and delegated level of authority. This will typically be the point at which the project is formally handed over to the owner and responsibility is transferred from the project team to the operational line management team.
Actions
Review and approve
Construction or implementation reviewed and approved by the delegated authority.
Deliverables
Construction projects completed:
- to meet detailed design engineering;
- to meet required construction practices;
- to cost, and
- to schedule.
Non-construction projects completed:
- to meet detailed implementation plan;
- to cost, and
- to schedule.
Project handed over to owner who is ready, willing and able to accept and operate it.
Agreed items to be addressed post start-up.
Frequency
As required by the schedule.
Guidance notes:
The construction or implementation should:
- for construction projects, be completed:
- to meet detailed design engineering;
- to meet required construction practices;
- to cost, and
- to schedule.
- for non-construction projects be completed:
- to meet detailed design implementation plan;
- to cost, and
- to schedule.
The project should be handed over to an owner who is ready, willing and competent to operate it. The handover should include a list of agreed outstanding items which will be addressed post start-up.
Throughout the construction/implementation any changes to the approved detailed design engineering and detailed implementation plan should be subjected to thorough assessment of the risks arising from these changes, in accordance with the MoC risk assessment guidelines as defined in steps 5 – 15.
All changes to the approved detailed design engineering and detailed implementation plan should be approved by appropriate nominated personnel with the necessary competency and delegated level of authority.
When the construction/implementation is completed, the completion status should be formally reviewed and accepted by the appropriate line manager with the necessary competency and delegated level of authority. This will typically be the point at which the project is formally handed over to the owner and responsibility is transferred from the project team to the operational line management team.
Actions
Operate and assess impact
Deliverables
Project incorporated into 'business as usual'. Review of overall project performance:
- against agreed investment business case:
- business benefits delivery, and
- cost and schedule.
- what went well, and
- what needs to be improved.
Formal close out of project with agreement, funding and agreed responsibility for justified necessary follow-up work to:
- deliver investment business case;
- address operability or maintainability issues, and
- resolve identified technical queries.
Frequency
As required by the schedule.
Guidance notes:
Following the construction/implementation and handover to the owner, the project should be:
- commissioned in accordance with Guidance on meeting expectations of EI Process safety framework Element 13: Operational readiness and process start-up.
- incorporated into 'business as usual' operation.
The agreed list of outstanding items to be addressed post start-up should be tracked to completion.
The change risk assessment should be updated to take into account the project as built/ as implemented.
In advance of final close out of the project, a formal assessment should be carried out to:
- verify that the project is delivering business benefits in accordance with the approved incentives to progress the project;
- verify that outstanding items have been completed as agreed;
- verify that identified necessary control measures have been implemented;
- identify lessons learned from the project development and implementation:
- what went well;
- what needs to be improved, and
- identify and agree responsibility and resource allocation for necessary follow-up activities.
More than one review may be appropriate, e.g. for organisational change it may be appropriate to carry out an initial review of the change impact and then a subsequent one six months later to confirm the design intent of the change has been achieved with no unexpected impacts.
The formal assessment of the project should involve representatives of the project owner and representatives of the project team.
The completed formal assessment of the project, and the agreed necessary follow-up actions, should be formally reviewed and accepted by the appropriate line manager with the necessary competency and delegated level of authority. This will typically be the point at which the project is finally closed out and all operation, maintenance and follow up activities become part of 'business as usual'.
Actions
Review and approve
Deliverables
Project incorporated into 'business as usual'. Review of overall project performance:
- against agreed investment business case:
- business benefits delivery, and
- cost and schedule.
- what went well, and
- what needs to be improved.
Formal close out of project with agreement, funding and agreed responsibility for justified necessary follow-up work to:
- deliver investment business case;
- address operability or maintainability issues, and
- resolve identified technical queries.
Frequency
As required by the schedule.
Guidance notes:
Following the construction/implementation and handover to the owner, the project should be:
- commissioned in accordance with Guidance on meeting expectations of EI Process safety framework Element 13: Operational readiness and process start-up.
- incorporated into 'business as usual' operation.
The agreed list of outstanding items to be addressed post start-up should be tracked to completion.
The change risk assessment should be updated to take into account the project as built/ as implemented.
In advance of final close out of the project, a formal assessment should be carried out to:
- verify that the project is delivering business benefits in accordance with the approved incentives to progress the project;
- verify that outstanding items have been completed as agreed;
- verify that identified necessary control measures have been implemented;
- identify lessons learned from the project development and implementation:
- what went well;
- what needs to be improved, and
- identify and agree responsibility and resource allocation for necessary follow-up activities.
More than one review may be appropriate, e.g. for organisational change it may be appropriate to carry out an initial review of the change impact and then a subsequent one six months later to confirm the design intent of the change has been achieved with no unexpected impacts.
The formal assessment of the project should involve representatives of the project owner and representatives of the project team.
The completed formal assessment of the project, and the agreed necessary follow-up actions, should be formally reviewed and accepted by the appropriate line manager with the necessary competency and delegated level of authority. This will typically be the point at which the project is finally closed out and all operation, maintenance and follow up activities become part of 'business as usual'.
Actions
Close out project
Deliverables
Project incorporated into 'business as usual'. Review of overall project performance:
- against agreed investment business case:
- business benefits delivery, and
- cost and schedule.
- what went well, and
- what needs to be improved.
Formal close out of project with agreement, funding and agreed responsibility for justified necessary follow-up work to:
- deliver investment business case;
- address operability or maintainability issues, and
- resolve identified technical queries.
Frequency
As required by the schedule.
Guidance notes:
Following the construction/implementation and handover to the owner, the project should be:
- commissioned in accordance with Guidance on meeting expectations of EI Process safety framework Element 13: Operational readiness and process start-up.
- incorporated into 'business as usual' operation.
The agreed list of outstanding items to be addressed post start-up should be tracked to completion.
The change risk assessment should be updated to take into account the project as built/ as implemented.
In advance of final close out of the project, a formal assessment should be carried out to:
- verify that the project is delivering business benefits in accordance with the approved incentives to progress the project;
- verify that outstanding items have been completed as agreed;
- verify that identified necessary control measures have been implemented;
- identify lessons learned from the project development and implementation:
- what went well;
- what needs to be improved, and
- identify and agree responsibility and resource allocation for necessary follow-up activities.
More than one review may be appropriate, e.g. for organisational change it may be appropriate to carry out an initial review of the change impact and then a subsequent one six months later to confirm the design intent of the change has been achieved with no unexpected impacts.
The formal assessment of the project should involve representatives of the project owner and representatives of the project team.
The completed formal assessment of the project, and the agreed necessary follow-up actions, should be formally reviewed and accepted by the appropriate line manager with the necessary competency and delegated level of authority. This will typically be the point at which the project is finally closed out and all operation, maintenance and follow up activities become part of 'business as usual'.
Actions
Stop project
Stop project if necessary following review.
Deliverables
Updated risk register taking into account implications of not progressing the project.
Archived project files.
Frequency
As required.
Guidance notes:
In situations where the incentives to progress the project are not justified, or the risks associated with the change cannot be managed to a defined level (e.g. tolerable), it may be necessary to make the decision to halt the development and implementation of the project.
In cases where the decision is taken to stop the project, the risks associated with this course of action should be identified and assessed.
Decisions to halt the development and implementation of the project should be reviewed and approved by the appropriate line manager with the necessary competency and delegated level of authority.
Decisions to halt the development and implementation of the project may typically require the identification and implementation of alternative control measures to manage the risks associated with the issue that the project was initiated to address.
Actions
Define scope of the change
Deliverables
All changes identified and the scope of each change defined, identifying:
- what will be changed;
- what will be impacted by the change, and
- who will be impacted by the change.
Changes reviewed and classified as either:
- high risk, or
- low risk.
Classifications are reviewed and approved by designated competent personnel.
Frequency
As required.
Guidance notes:
All changes should be identified, clearly defining:
- the change category (in accordance with the criteria defined in step 3);
- what will be changed, and
- what or who will be impacted by the change.
All identified changes should be reviewed and classified as either high risk or low risk (in accordance with the criteria defined in step 3).
The categorisation and classification should be reviewed and approved by appropriate nominated personnel with the necessary competency and delegated level of authority.
An example template for the initial assessment and classification of a change is shown in Annex E.
Actions
Initial assessment
Deliverables
All changes identified and the scope of each change defined, identifying:
- what will be changed;
- what will be impacted by the change, and
- who will be impacted by the change.
Changes reviewed and classified as either:
- high risk, or
- low risk.
Classifications are reviewed and approved by designated competent personnel.
Frequency
As required.
Guidance notes:
All changes should be identified, clearly defining:
- the change category (in accordance with the criteria defined in step 3);
- what will be changed, and
- what or who will be impacted by the change.
All identified changes should be reviewed and classified as either high risk or low risk (in accordance with the criteria defined in step 3).
The categorisation and classification should be reviewed and approved by appropriate nominated personnel with the necessary competency and delegated level of authority.
An example template for the initial assessment and classification of a change is shown in Annex E.
Actions
Review and approve
Review and approve initial assessment.
Deliverables
All changes identified and the scope of each change defined, identifying:
- what will be changed;
- what will be impacted by the change, and
- who will be impacted by the change.
Changes reviewed and classified as either:
- high risk, or
- low risk.
Classifications are reviewed and approved by designated competent personnel.
Frequency
As required.
Guidance notes:
All changes should be identified, clearly defining:
- the change category (in accordance with the criteria defined in step 3);
- what will be changed, and
- what or who will be impacted by the change.
All identified changes should be reviewed and classified as either high risk or low risk (in accordance with the criteria defined in step 3).
The categorisation and classification should be reviewed and approved by appropriate nominated personnel with the necessary competency and delegated level of authority.
An example template for the initial assessment and classification of a change is shown in Annex E.
Actions
High risk change
Determine if the change is a high risk or low risk change.
Deliverables
All changes identified and the scope of each change defined, identifying:
- what will be changed;
- what will be impacted by the change, and
- who will be impacted by the change.
Changes reviewed and classified as either:
- high risk, or
- low risk.
Classifications are reviewed and approved by designated competent personnel.
Frequency
As required.
Guidance notes:
All changes should be identified, clearly defining:
- the change category (in accordance with the criteria defined in step 3);
- what will be changed, and
- what or who will be impacted by the change.
All identified changes should be reviewed and classified as either high risk or low risk (in accordance with the criteria defined in step 3).
The categorisation and classification should be reviewed and approved by appropriate nominated personnel with the necessary competency and delegated level of authority.
An example template for the initial assessment and classification of a change is shown in Annex E.
Actions
Risk assessment
For low risk changes.
Deliverables
Completed change risk assessment.
Risks identified and assessed.
Identified control measures to manage risk to a defined (e.g. tolerable) level.
Frequency
As required.
Actions
Risk assessment
For high risk changes.
Deliverables
Completed change risk assessment.
Risks identified and assessed.
Identified control measures to manage risk to a defined (e.g. tolerable) level.
Frequency
As required.
Actions
Define control measures
For low risk changes.
Deliverables
Completed change risk assessment.
Risks identified and assessed.
Identified control measures to manage risk to a defined (e.g. tolerable) level.
Frequency
As required.
Actions
Define control measures
For high risk changes.
Deliverables
Completed change risk assessment.
Risks identified and assessed.
Identified control measures to manage risk to a defined (e.g. tolerable) level.
Frequency
As required.
Actions
Safe operations committee review of high risk changes
Deliverables
High risk changes reviewed and approved for review by safe operations committee.
Approved low risk changes (formally documented).
Rejected changes (formally documented).
Frequency
As required.
Actions
Review and approve
Management review and approval of control measures.
Deliverables
Approved high risk changes.
Rejected high risk changes.
Frequency
As required.
Guidance notes:
High risk changes
Changes classified as high risk should be assessed, in accordance with the criteria defined in Step 3, and identified the necessary control measures to achieve a defined (e.g. tolerable) level of risk.
The risk assessment methods should make use of appropriate guidelines for the elements which are applicable to the changes proposed, such as:
- Element 6: Hazard identification and risk assessment;
- Element 3: Employee selection, placement and competency, and health assurance, and
- Element 17: Work control, permit to work and task risk management.
Examples of worksheets for use in organisational change risk assessment are shown in Annex F and Annex G.
The completed assessment should identify:
- the unmitigated risk;
- the necessary control measures, and
- the mitigated risk level.
The completed risk assessments for high risk changes should be reviewed by independent competent persons who together have experience across the range of disciplines necessary to assure process safety. Typically these would include operations, maintenance, process design, training and development, HS&E and line management. It can be helpful to establish a 'safe operations committee' with a constituency which includes the relevant specialists who can, on behalf of the organisation, carry out this independent review of high risk changes.
It should be checked whether there are regulatory requirements to consult with specific members of the owner group; for example, in the GB there is a regulatory requirement to consult safety representatives on health and safety issues.
For high risk changes, steps 11 and 12 may be combined, with the appropriate line manager (with the necessary competency and delegated level of authority) participating in the safe operating committee review, and, taking into account the outcome of the safe operating committee review, either approving or rejecting the proposed change.
Low risk changes
Changes classified as low risk should be assessed, in accordance with the criteria defined in step 3, and the necessary control measures to achieve a defined (e.g. tolerable) level of risk should be identified.
The completed assessment should identify:
- the unmitigated risk;
- the necessary control measures, and
- the mitigated risk level.
The completed risk assessments for low risk changes should be reviewed and approved by an appropriate line manager with the necessary competency and delegated level of authority.
Actions
Implement approved control measures
Deliverables
Approved control measures implemented in full and to schedule.
Risk of change controlled to a defined (e.g. tolerable) level.
Frequency
As required by schedule.
Guidance notes:
If the change is approved, the required control measures should be implemented in full and in line with the required schedule to ensure that the identified risks associated with the change are managed to a defined (e.g. tolerable) level.
Responsible line managers should check to ensure that the required control measures have been implemented.
Actions
Revise control measures
Deliverables
Decision that:
- control measures should be revised in order to achieve defined (e.g. tolerable) risk;
- alternative approach to the change should be adopted in order to achieve defined (e.g. tolerable) risk, or
- defined (e.g. tolerable) risk cannot be achieved and the change should not be progressed.
Frequency
As required.
Guidance notes:
In cases where the change assessment is not approved, an alternative approach or revised control measures should be considered. These should be reviewed and approved appropriately as described in steps 10a/10b – 12.
In cases where an alternative approach or revised control measures are not feasible it may be necessary to reject the proposed change.
Actions
Update records
Deliverables
Records updated to:
- create and maintain MoC register;
- reflect post-project implementation situation, and
- meet requirements of Guidance on meeting expectations of EI Process safety framework Element 7: Documentation, records and knowledge management.
Frequency
As required by the schedule.
Guidance notes:
Records should be updated in accordance with the requirements of Guidance on meeting expectations of EI Process safety framework Element 7: Documentation, records and knowledge management.
The records should include a MoC register, which maintains an up-to-date register of all changes, covering at minimum: a unique identifier; a description of the change; a description of the reason for the change; the person initiating the change; the current status of the change, and the identified necessary control measures. The records should cover both approved and rejected changes.
The element owner should ensure that a custodian is appointed for the MoC register, who has responsibility for ensuring that the MoC register is created, maintained up-todate and readily available to those personnel who need to be aware of it and make use of it.
Actions
Performance measurement and compliance checking
Establish and implement PMs.
Establish regular management and supervisory compliance checks.
Deliverables
Defined PMs generated in line with the schedule.
Compliance checking programme.
Completed compliance checks.
Identified necessary interventions.
Frequency
As required by the schedule.
Guidance notes:
A systematic set of PMs should be defined in order to enable each BU or site to monitor and confirm compliance with the element and to draw attention to any areas of noncompliance.
In order to maintain effective control, the element owner should ensure that accountability for performance against each PM is clearly identified and that the accountable person understands the interventions that need to be made to correct deviations in performance against the PM.
The element owner should ensure that PMs are reviewed by an appropriate level of management on a routine scheduled basis.
The suggested PMs are defined in section 3.
Actions
Performance and compliance trend analysis
PMs and findings from compliance checks are analysed to identify any emerging underlying trends.
Deliverables
A report on trends identified, for review:
- at appropriate management meetings;
- by BU executive, and
- by company executive.
Frequency
Monthly.
Guidance notes:
Section 3 defines suggested PMs which may allow the BU or site to monitor compliance with the element. This is an important aspect of management control but it does not provide the whole picture. Findings from compliance checking and performance monitoring should be reviewed and analysed in order to identify any underlying trends. The trends that should be monitored and analysed should be adapted according to performance and the issues being managed during any particular time period. However, it is important to ensure that resource is assigned to carry out this monitoring and analysis and that this trend analysis is carried out on a routine basis and presented for review at appropriate management meetings.
Actions
Annual review of effectiveness and sustainability of element arrangements
Review of the arrangements to check that they are functioning as intended and are still fit-for-purpose.
Deliverables
A report identifying:
- issues requiring resolution, and
- opportunities to enhance the arrangements.
Frequency
Annually.
Guidance notes:
The element owner should initiate an annual review of the element in order to check that it is still functioning as intended and that it is still-fit-for purpose, identifying any issues requiring resolution or any opportunities to enhance the implementation of the element.
The element owner should ensure that appropriate employees and employees’ representatives are involved in developing input to this review.
Actions
Management review and control meetings
Review meetings with the appropriate levels of management.
Systematic review of defined PM sets.
Review emerging issues identified by the analysis of trends.
Manage issues and opportunities identified by annual review of the process.
Identify appropriate interventions.
Deliverables
PMs and trend analysis reviewed:
- at appropriate management meetings;
- by local line management;
- by BU executive, and
- by company executive.
Appropriate interventions to correct deviations from required performance.
Initiation of appropriate actions to address findings from the annual review.
Frequency
Monthly.
Guidance notes:
The element owner should ensure that the review of the PMs is incorporated into appropriate management control meetings. It is likely that it will be necessary to incorporate the PMs into meetings at a number of different levels. For example, they may need to be incorporated into executive meetings and into senior management team meetings. Understandably, the scope of the PM should be matched to the area of the organisation which is being reviewed at each meeting.
The management control meetings should focus on deviations from the required performance, identifying necessary interventions to correct the performance.
The PMs and the output from these management control meetings may provide input to appropriate health and safety committees.
3. Suggested compliance checks and performance measures
This guideline provides a set of suggested implementation and operational PMs.
The implementation PMs can be used for the implementation phase to measure and monitor the backlog (clear up) tasks that are required. The operational PMs can be used to measure compliance with the element as part of business as usual.
In order to be confident that control measures are being implemented appropriately, it should be ensured that there are regular routine management and supervisory field observations carried out by line management and supervision. Some of the suggested operational PMs are derived from the results of these observations.
The required frequency of measurement and checking may vary according to the level of demonstrated performance. If the performance of a parameter is demonstrated to be under control then the measurement and checking interval may be extended. However, if the performance of the parameter is shown to be unacceptable the interval should be reduced. It should be ensured that there is a frequency of measurement and checking which assures an appropriate level of control.
Table 1: Performance measures for element 12
No. | Type | Performance Measure |
---|---|---|
1 | Implementation and compliance | Element compliance and implementation status (EIPSS rating) |
2 | Operational | Number of changes reviewed, categorised by type |
3 | Operational | Number of changes reviewed, categorised by potential impact |
4 | Operational | MoC assessments overdue |
5 | Operational | Implementation of identified MoC control measures overdue |
6 | Operational | Number of temporary changes in place at month end |
7 | Operational | Number of temporary changes exceeding original authorisation period |
8 | Operational | HS&E projects status – forecast status against schedule |
9 | Operational | Observed non-compliance with MoC and project management requirements |
10 | Operational | Overdue field observations |
11 | Outcome | Incident root causes which are failures of element 12 |
3.1 Performance measure 1: Element compliance and implementation status (EIPSS rating)
This PM enables management to monitor the implementation and compliance of the element of the EI PSM framework. It makes use of the EI Process Safety Survey (EIPSS) to enable the business to carry out a systematic self-assessment of their compliance with the expectations of element 12.
The EIPSS can be used for a base line assessment of compliance, which can then be updated as those responsible close each of the individual identified gaps. In this way it provides management with an easily developed continuously updated assessment of implementation and compliance.
The line manager accountable for implementation should make a corrective intervention if the actual progress falls below plan. It is likely the required interventions would be either to adjust priorities to create space to allow this work to be done, to make additional resource available or to reset the schedule to reflect what can be achieved realistically with the assigned resource.
Table 2: Element compliance and implementation status (EIPSS rating) – PM overview
Type | Required data | Representation |
---|---|---|
Implementation and compliance | By month:
|
Line and bar graph:
|
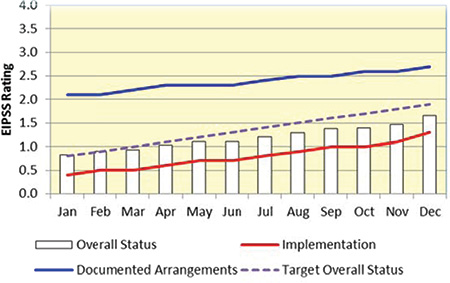
Figure 3: Suggested presentation of PM 1: Element compliance and implementation status (EIPSS rating)
3.2 Performance measure 2: Number of changes reviewed, categorised by type
This PM enables management to monitor the volume of changes being reviewed and classified by type. Within the work area it is likely that this PM would be supported by a list showing each of the changes, when the initial risk assessment was completed, the control measure proposed for that change, and who the responsible line managers are in each case.
The accountable line manager should consider the need to make an intervention if there is an increasing trend or a continued large number of changes.
It is likely that the required intervention would be to probe the business justification for the changes, to ensure that only fully justified changes are being progressed. The accountable line manager should also ensure that any increase in the numbers of changes being progressed is not compromising the effectiveness and quality of the change management assessment and controls, and that there is sufficient resource allocated to manage the number of changes being progressed.
Table 3: Number of changes reviewed, categorised by type – PM overview
Type | Required data | Representation |
---|---|---|
Operational | By month:
|
Stacked bar
|
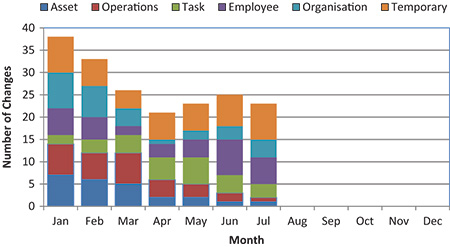
Figure 4: Suggested presentation of PM 2: Number of changes reviewed, categorised by type
3.3 Performance measure 3: Number of changes reviewed, categorised by potential impact
This PM enables management to monitor the volume of changes being reviewed, classified by potential impact (unmitigated) using the risk matrices (in accordance with Guidance on meeting expectations of EI Process safety management framework Element 6: Hazard identification and risk assessment, and Guidance on meeting expectations of EI Process safety management framework Element 19: Incident reporting and investigation). Within the work area it is likely that this PM would be supported by a list showing each of the changes, when the initial risk assessment was completed and who the responsible line managers are in each case.
The accountable line manager should consider the need to make an intervention if there is an increasing trend or a continued large number of changes. They should also consider the need to make an intervention if the potential impact shows an increasing trend.
It is likely that the required intervention would be to probe the business justification for the changes, to ensure that only fully justified changes are being progressed. The accountable line manager should also ensure that any increase in the numbers of changes being progressed is not compromising the effectiveness and quality of the change management assessment and controls, and that there is sufficient resource allocated to manage the number of changes being progressed.
Table 4: Number of changes reviewed, categorised by potential impact – PM overview
Type | Required data | Representation |
---|---|---|
Operational | By month:
|
Stacked bar:
|
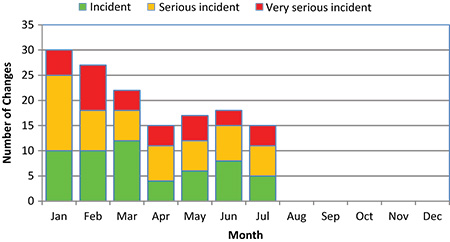
Figure 5: Suggested presentation of PM 3: Number of changes reviewed, categorised by potential impact
3.4 Performance measure 4: MoC assessments overdue
This PM enables management to monitor the number of MoC assessments that are overdue, tracking the number that are overdue by less than one month and the number that are overdue by more than one month.
The graphical representation of this PM is likely to be supplemented by a listing of the overdue MoC assessments, together with the responsible line manager and the reasons in each case.
The accountable line manager should make an intervention if there are any MoC assessments that are overdue.
It is likely that the required intervention would be to directly request the appropriate line manager to ensure that the outstanding MoC assessments are completed before the next management control meeting and to investigate why they were not done and what needs to be done to ensure that they are done in future. Typically, this may require adjustment of priorities to create space to allow this work to be done, or making additional resource available. If the situation continues for some time it is likely to be indicative of an underlying issue with either resource levels or planning, scheduling and supervision of the work activities.
Table 5: MoC assessments overdue – PM overview
Type | Required data | Representation |
---|---|---|
Operational | By month:
|
Stacked bar graph
|
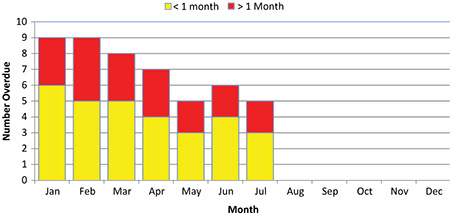
Figure 6: Suggested presentation of PM 4: MoC assessments overdue
3.5 Performance measure 5: Implementation of identified MoC control measures overdue
This PM enables management to monitor the number of MoC control measures that are overdue for implementation, tracking the number that are overdue by less than one month and the number that are overdue by more than one month.
The graphical representation of this PM is likely to be supplemented by a listing of the MoC control measures that are overdue for implementation, together with the responsible line manager and the reasons in each case.
The accountable line manager should make an intervention if there are any MoC control measures that are overdue for implementation.
It is likely that the required intervention would be to directly request the appropriate line manager to ensure that the implementation of any outstanding MoC control measures is completed before the next management control meeting and to investigate to find out why they were not done and what needs to be done to ensure that they are done in future. If the situation continues for some time it is likely to be indicative of an underlying issue with either resource levels or planning, scheduling and supervision of the work activities.
Table 6: Implementation of identified MoC control measures overdue – PM overview
Type | Required data | Representation |
---|---|---|
Operational | By month:
|
Stacked bar graph
|
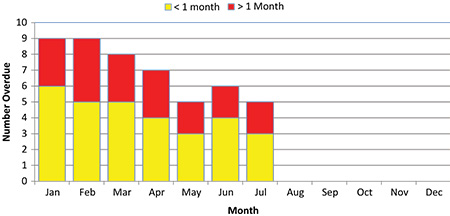
Figure 7: Suggested presentation of PM 5: Implementation of identified MoC control measures overdue
3.6 Performance measure 6: Number of temporary changes in place at month end
This PM enables management to monitor the number of temporary changes which are in place, tracking the number of temporary changes in place for more than six months and the number in place for less than six months.
Within the work area it is likely that this PM would be supported by a list showing each of the temporary changes, when it was authorised, how long it has been in place and who the responsible line managers are in each case.
The accountable line manager should ensure that the number of temporary changes is maintained at a manageable level and should make an intervention if there is an increasing trend in the number of temporary changes, especially those in place for more than six months. It is likely that the intervention would be to request the responsible line managers to justify the business need for the temporary changes and to identify what support they need to close out the outstanding temporary changes. They may also consider increasing the number of field observations to confirm that the identified necessary control measures are in place and are effective.
Table 7: Number of temporary changes in place at month end – PM overview
Type | Required data | Representation |
---|---|---|
Operational | By month:
|
Stacked bar graph:
|
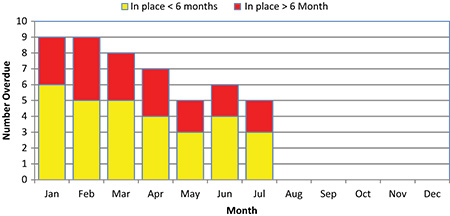
Figure 8: Suggested presentation of PM 6: Number of temporary changes in place at month end
This PM enables management to monitor the number of temporary changes which have been in place for longer than their original authorisation period, tracking the number that are authorised extensions and the number that are unauthorised-extensions.
The graphical representation of this PM is likely to be supplemented by a listing of the temporary changes which have been in place for longer than their original authorisation period, the original authorisation period, the history of any extensions, together with the responsible line manager and the reasons in each case.
The accountable line manager should make an intervention if there are any temporary changes which have been in place for longer than their original authorisation period.
In cases where the extension is unauthorised, it is likely that this should be reported as an incident and investigated in accordance with Guidance on meeting expectations of EI Process safety management framework Element 19: Incident reporting and investigation.
In cases where the extensions are authorised, the accountable line manager should make an intervention if there are specific cases where there are either long or repeated extensions of the authorised period. The intervention may be to directly request the appropriate line manager to identify what would be required to expedite a permanent solution to replace the temporary change.
In case of an overall increasing trend in the number of extensions it is likely that the first intervention would be to challenge the line managers to explain why it has been necessary to extend the authorisations rather than implement permanent solutions and to identify what help is required to close out the temporary changes.
Table 8: Number of temporary changes exceeding original authorisation period – PM overview
Type | Required data | Representation |
---|---|---|
Operational | By month:
|
Stacked bar graph:
|
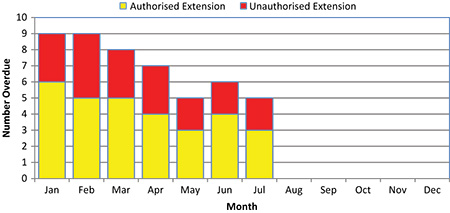
Figure 9: Suggested presentation of PM 7: Number of temporary changes exceeding original authorisation period
3.8 Performance measure 8: HS&E projects status – forecast status against schedule
This PM enables management to monitor forecast outcome of the live HS&E projects against the schedule, tracking the number that are forecast to be delivered:
- within one month of the scheduled date;
- more than one month behind schedule;
- more than three months behind schedule;
- more than one month ahead of schedule, and
- more than three months ahead of schedule.
The graphical representation of this PM is likely to be supplemented by a listing of the live HS&E projects, together with their original scheduled completion date, the current forecast completion date, the variation in months and the responsible manager.
The accountable line manager should make an intervention if there are any HS&E projects which are forecast to be more than one month behind schedule. It is likely that the intervention would be to request the responsible manager to identify what needs to be done and what support is required to get the project back on schedule, and to assess the process safety implications of the delay together with any necessary additional temporary control measures in order to ensure that the risk is maintained at a defined (e.g. tolerable) level if the schedule delay cannot be recovered.
In cases where the proportion of projects forecast to be delivered within one month of the scheduled date is low or decreasing, there may be an underlying problem with either the estimating, planning and scheduling techniques being applied or there may be an underlying problem with project execution. In this case the accountable line manager should consider initiating an investigation to identify whether there is an underlying issue and what needs to be done to correct it.
Table 9: HS&E projects status – forecast status against schedule – PM overview
Type | Required data | Representation |
---|---|---|
Operational | By month, number forecast:
|
Stacked bar graph:
|
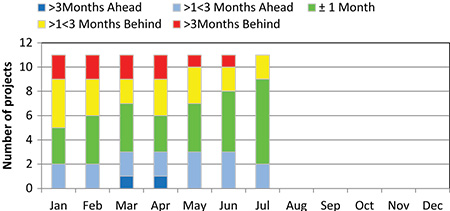
Figure 10: Suggested presentation of PM 8: HS&E projects status – forecast status against schedule
3.9 Performance measure 9: Observed non-compliance with MoC and project management requirements
This PM enables management to monitor the number of observed non-compliances with requirements for MoC and project management, tracking the number of observed major non-compliances and the number of observed minor non-compliances.
The graphical representation of this PM is likely to be supplemented by a listing of the observed major non-compliances together with the responsible line manager in each case.
The accountable line manager may need to make an intervention if there is a prolonged increasing trend in the number of non-compliances. It is likely that the intervention would be to question what additional support or resources would be required to correct the trend.
Table 10: Observed non-compliance with MoC and project management requirements – PM overview
Type | Required data | Representation |
---|---|---|
Operational | By month:
|
Stacked bar graph:
|
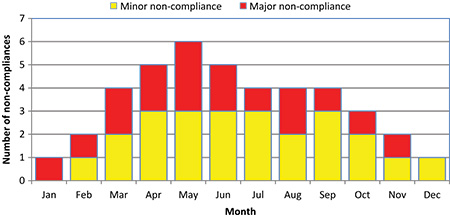
Figure 11: Suggested presentation of PM 9: Observed non-compliance with MoC and project management requirements
3.10 Performance measure 10: Overdue field observations
This PM enables management to monitor whether the scheduled management and supervisory field observations have been carried out, tracking the number of overdue field observations. It is likely that this PM would be supported by a list showing each of the overdue field observations and who the responsible line managers are in each case.
The accountable line manager should make an intervention if there are any overdue field observations.
It is likely that the required intervention would be to directly request the appropriate line manager to ensure that the outstanding field observations are completed before the next management control meeting and to question why they were not done and what needs to be done to ensure that they are done in future. Typically, this will require adjustment of priorities, reassigning work activities to create space to allow this work to be done. If the situation continues for some time it is likely to be indicative of an underlying issue with either resource levels or time planning.
Table 11: Overdue field observations – PM overview
Type | Required data | Representation |
---|---|---|
Operational | By month:
|
Bar graph |
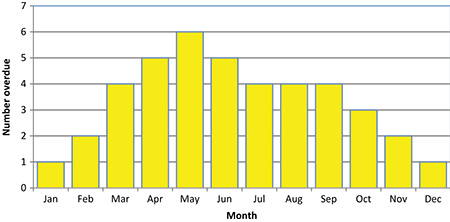
Figure 12: Suggested presentation of PM 10: Overdue field observations
3.11 Performance measure 11: Incident root causes which are failures of element 12
This PM enables management to monitor the trend of the number of times a failure of some aspect of element 12 is identified as a root cause of an incident (EI Guidance on meeting expectations of EI Process safety management framework Element 19: Incident reporting and investigation provides guidelines on how root causes should be aligned to failures of EI PSM framework elements). This information will assist line managers to understand whether the arrangements for meeting the expectations of element 12 are achieving the required outcome.
A constant or increasing number of root causes associated with a failure of this element would indicate that there is a need to review the effectiveness of the arrangements and their implementation.
Table 12: Incident root causes which are failures of element 12 – PM overview
Type | Required data | Representation |
---|---|---|
Outcome (lagging indicator) |
By month, number of incident root causes which are failures of element 12 categorised as root causes of:
|
Stacked bar:
|
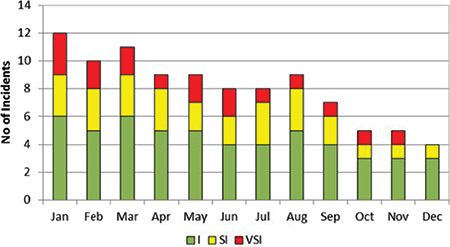
Figure 13: Suggested presentation of PM 11: Incident root causes which are failures of element 12
Annex A
Reference and bibliography
A.1 References
EI, High level framework for process safety management,
http://www.energyinst.org/psm-framework
A.2 Further resources
This section contains a non-exhaustive list of further resources to help organisations implement element 12. Resources include pertinent guidance publications, codes of practice, standards, and practical tools.
Description | Step | |
---|---|---|
CCPS | Guidelines for the management of change for process safety | 01, 14 |
HSE | HSG254, Developing process safety indicators, A step-by-step guide for the chemical and major hazard industries http://books.hse.gov.uk/hse/public/saleproduct.jsf?catalogueCode=9780717661800 | 16, 17 |
EI | Human factors briefing note no.3 – Organisational change | 02 |
Annex B
Glossary of acronyms and abbreviations
BI | business interruption |
BU | business unit |
E&R | environment and reputation |
EIPSS | Energy Institute Process Safety Survey |
H&S | health and safety |
HS&E | health, safety and environment |
HSE | Health and Safety Executive |
I | incident |
MAH | major accident hazard |
MoC | management of change |
PM | performance measure |
PSM | process safety management |
ROI | return on investment |
SI | serious incident |
VSI | very serious incident |
Annex C
Mapping of process steps to EI PSM framework expectations
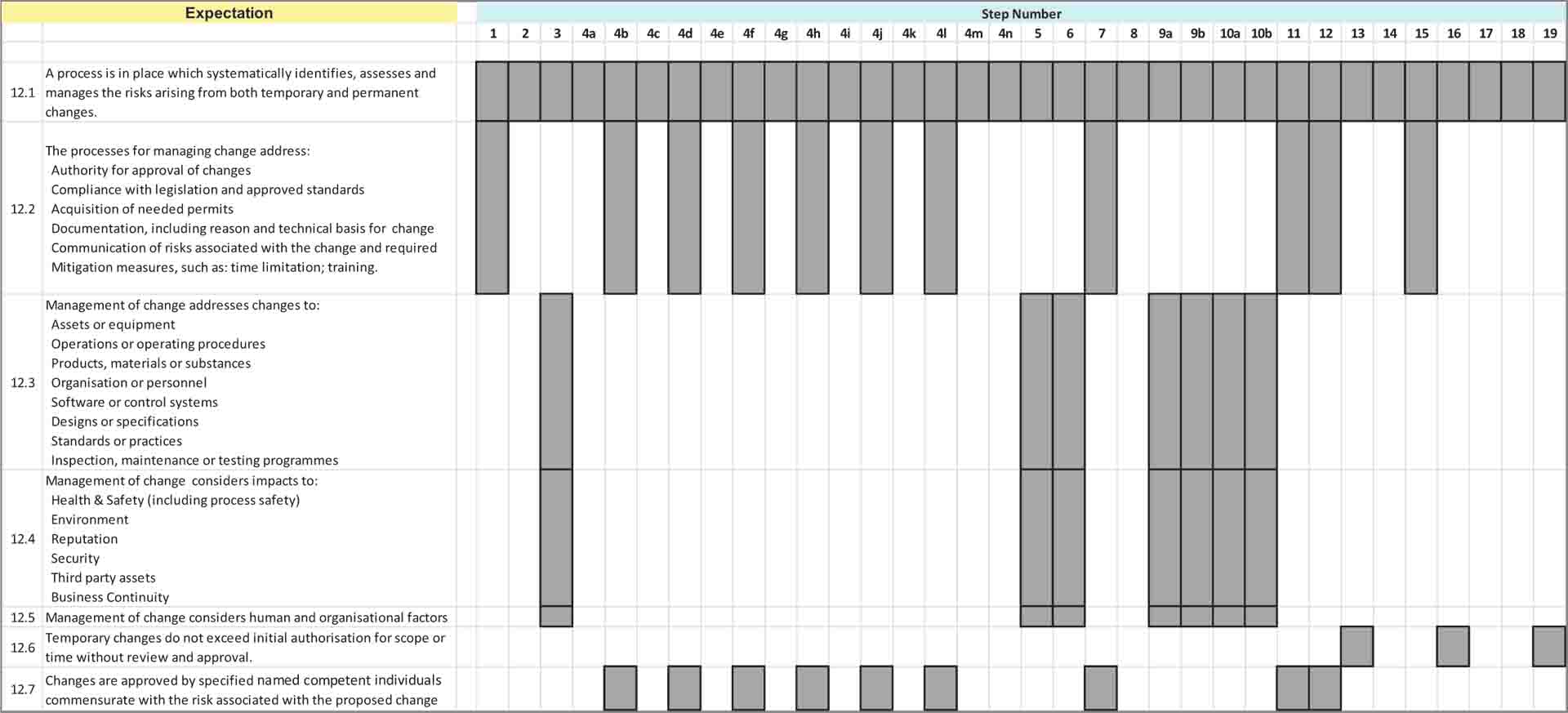
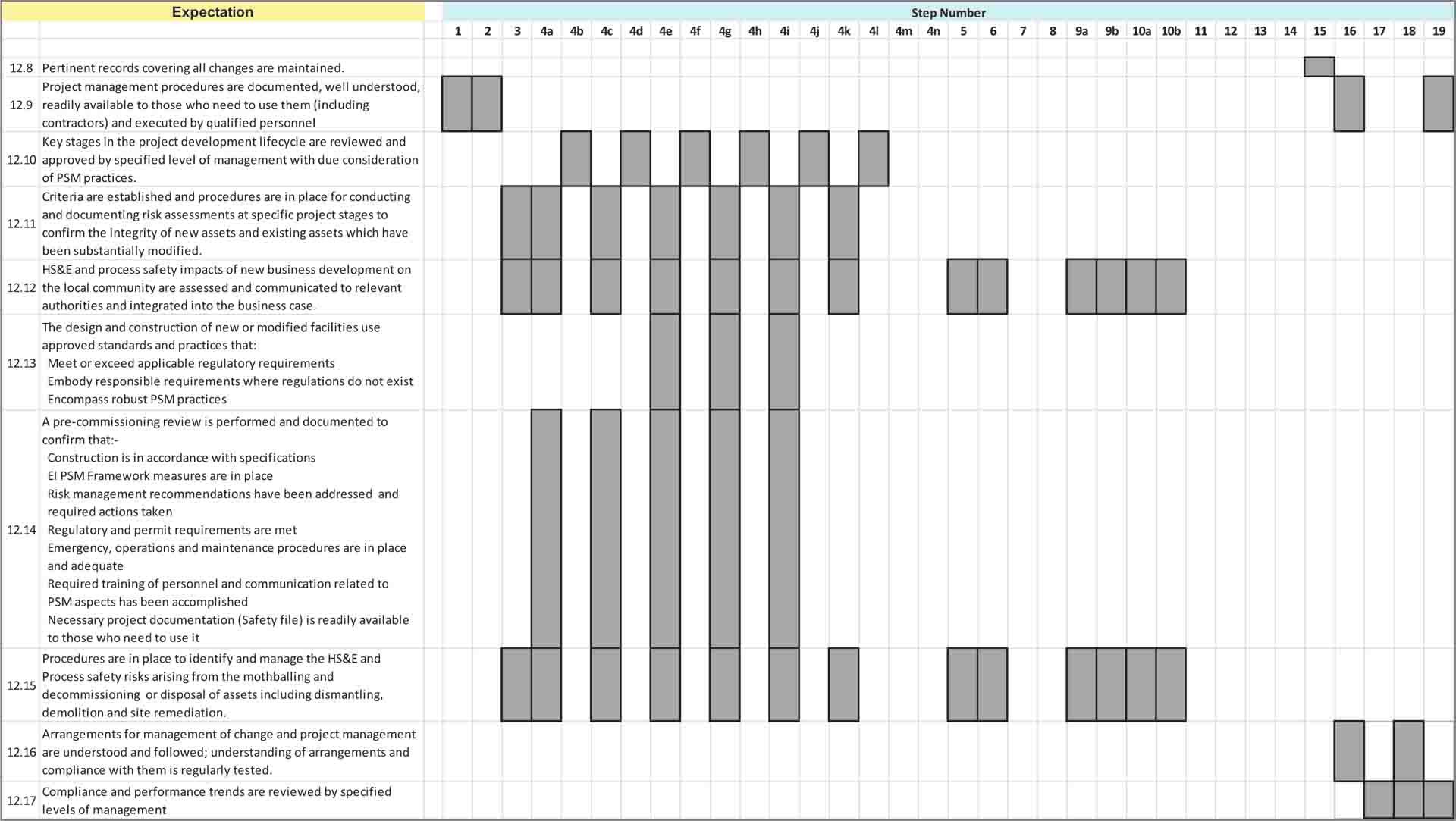
Annex D
Example report template: Management and supervisory field observation
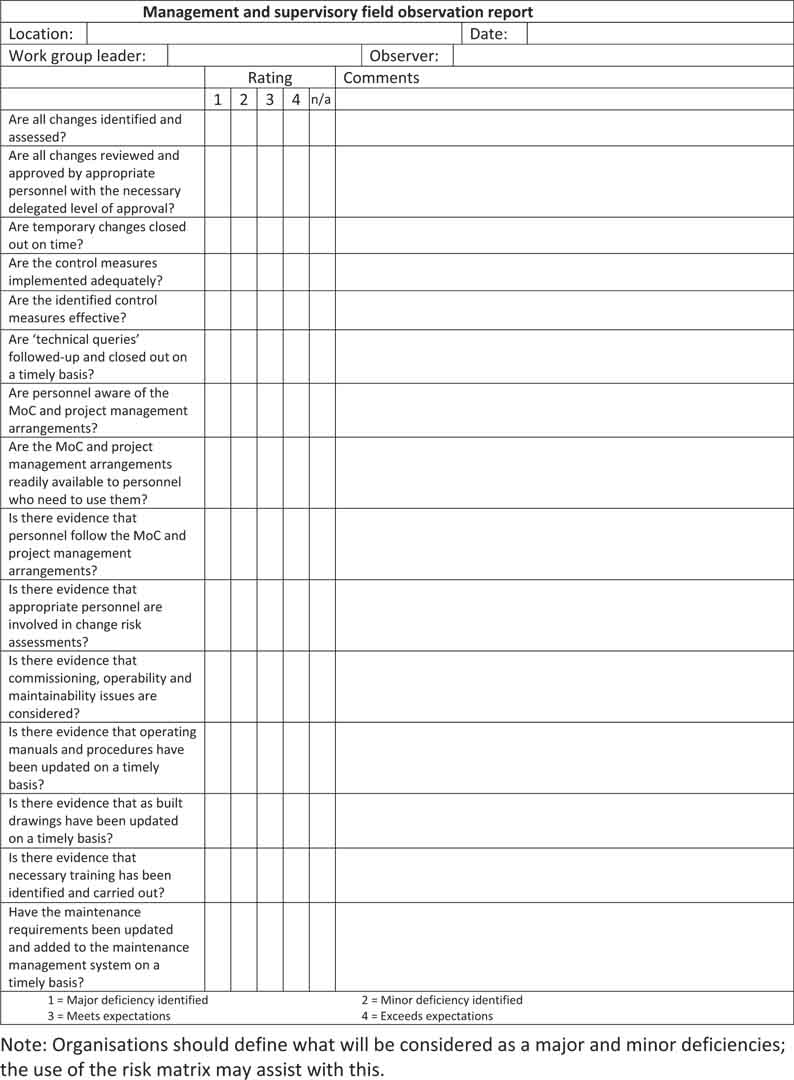
Annex E
Example template: Initial change risk assessment
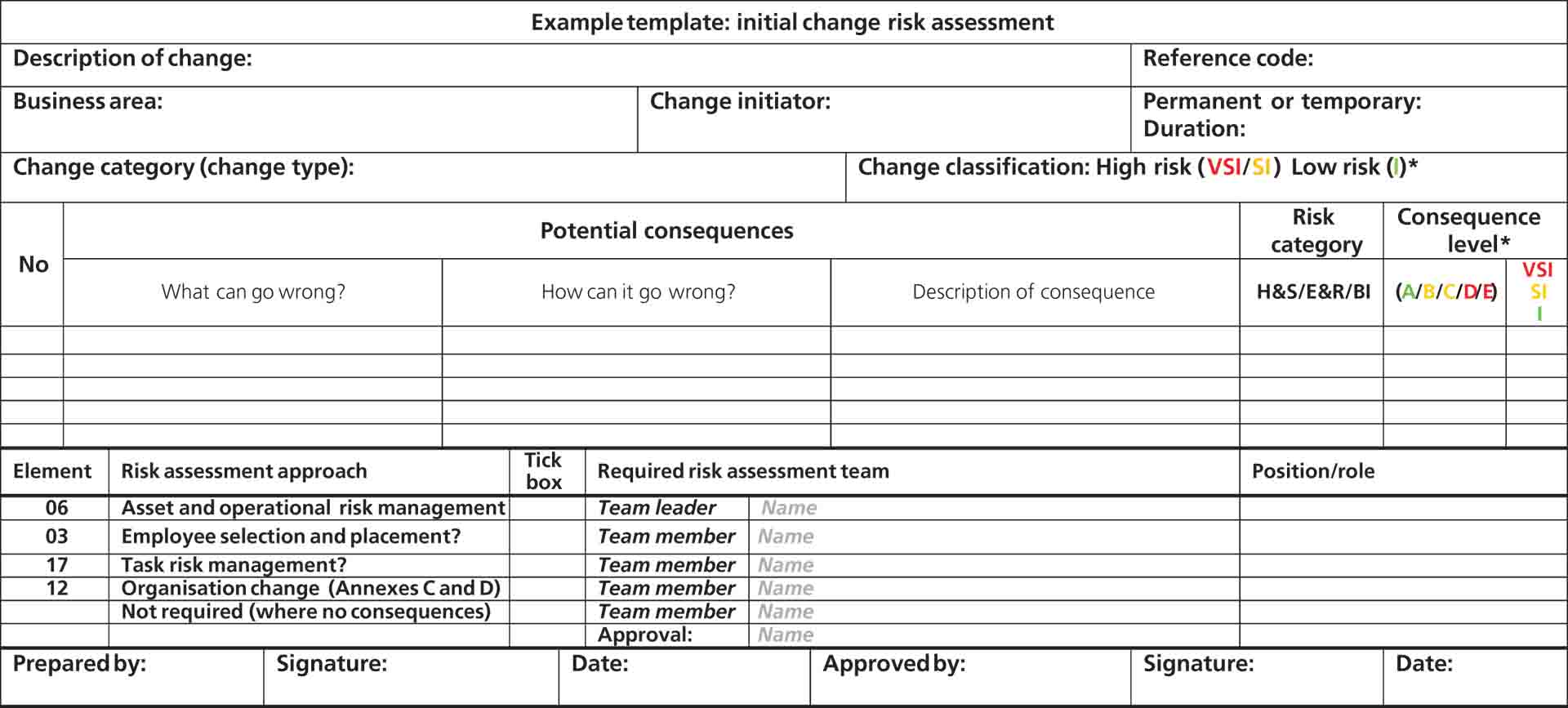
Annex F
Example template: Organisational change risk assessment worksheet – Position specific
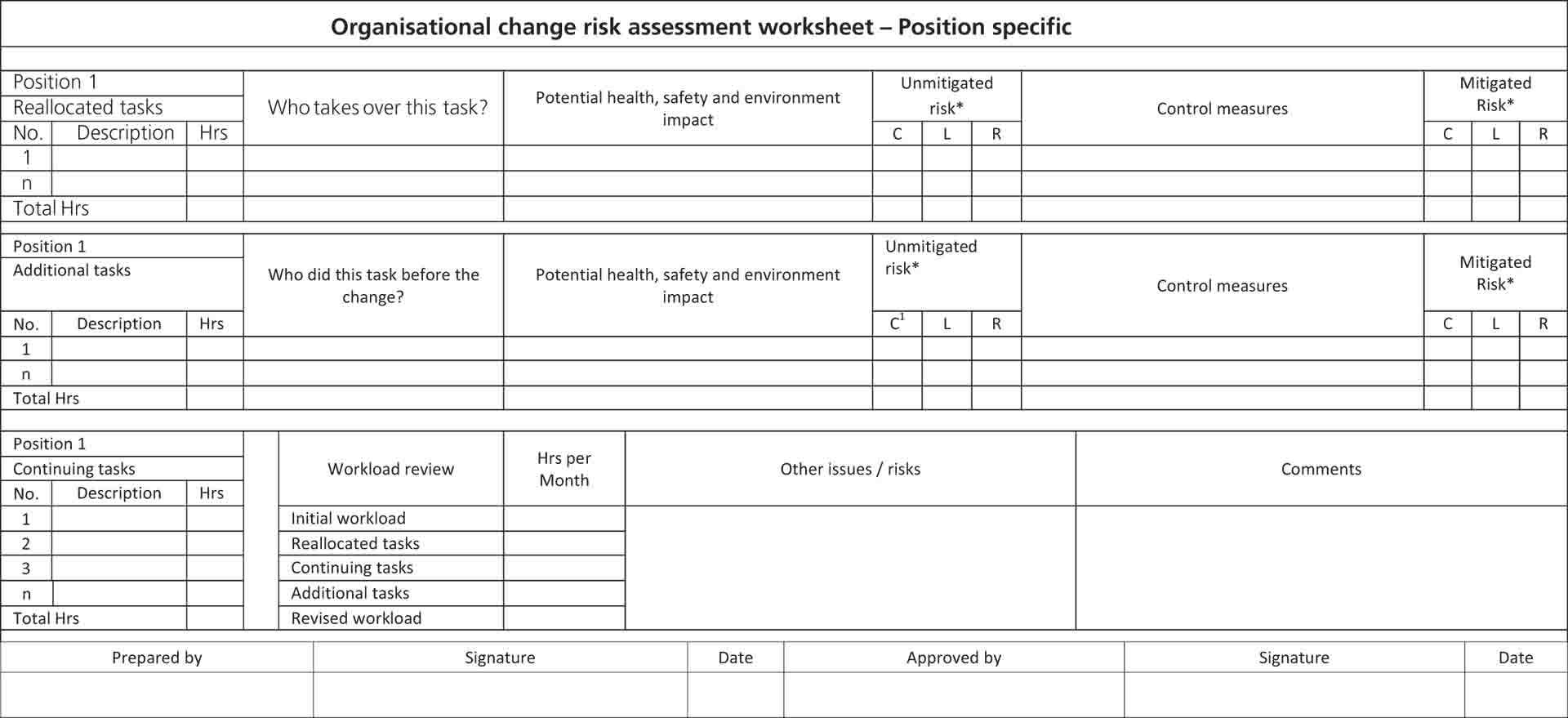
Annex G
Example template: Organisational change risk assessment worksheet – Resource balance assessment
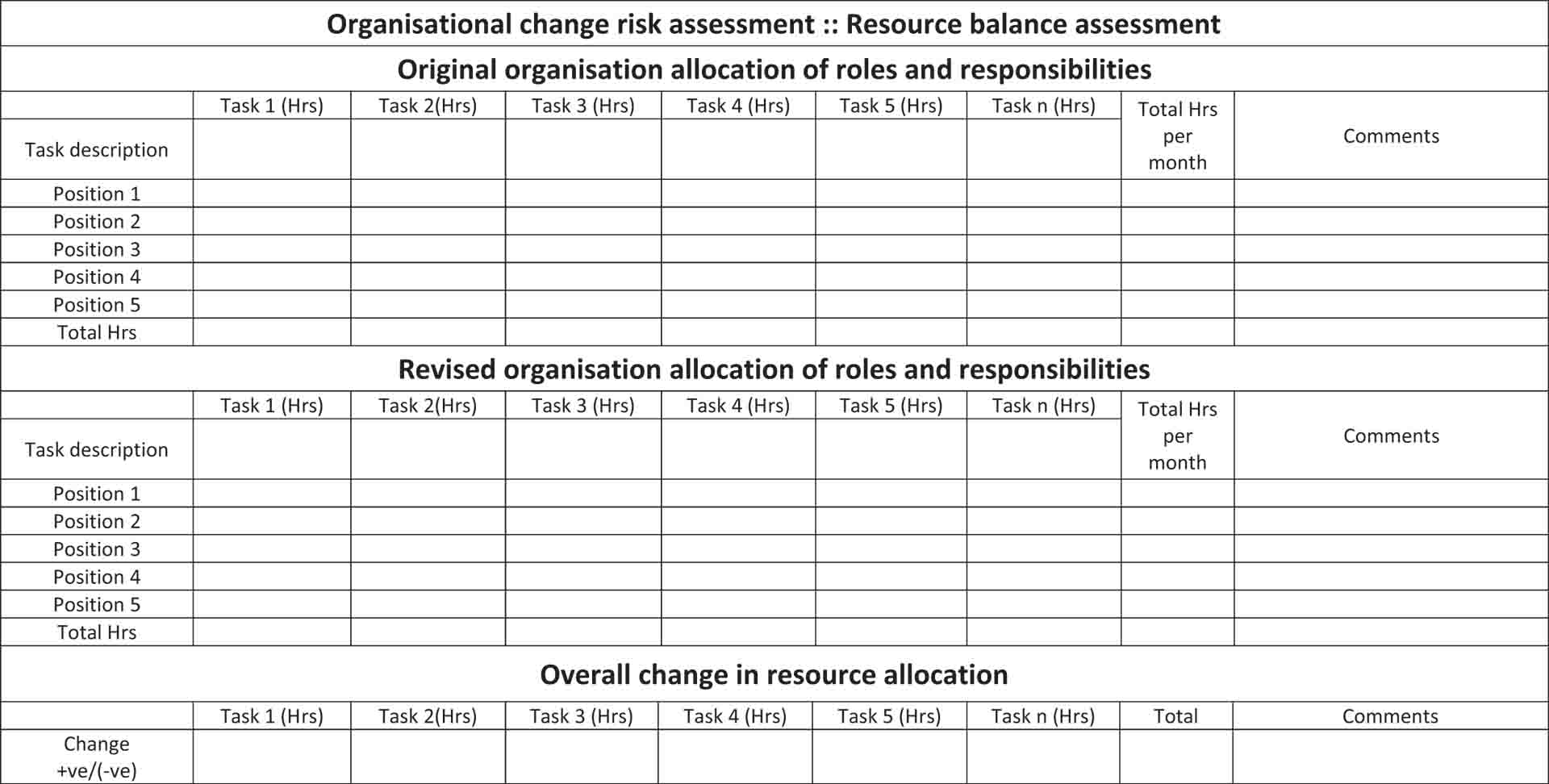
Annex H
Example risk and prioritisation matrices
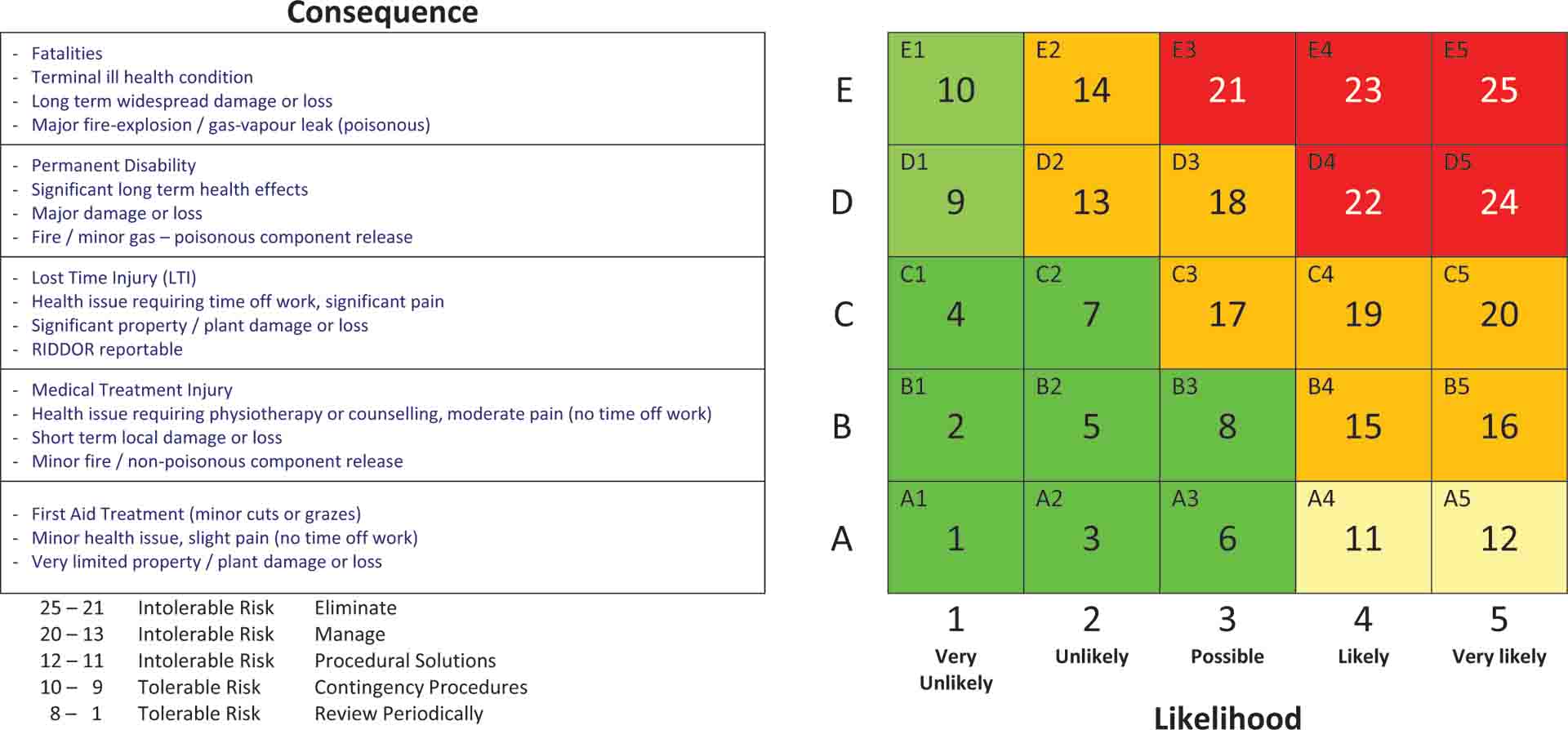
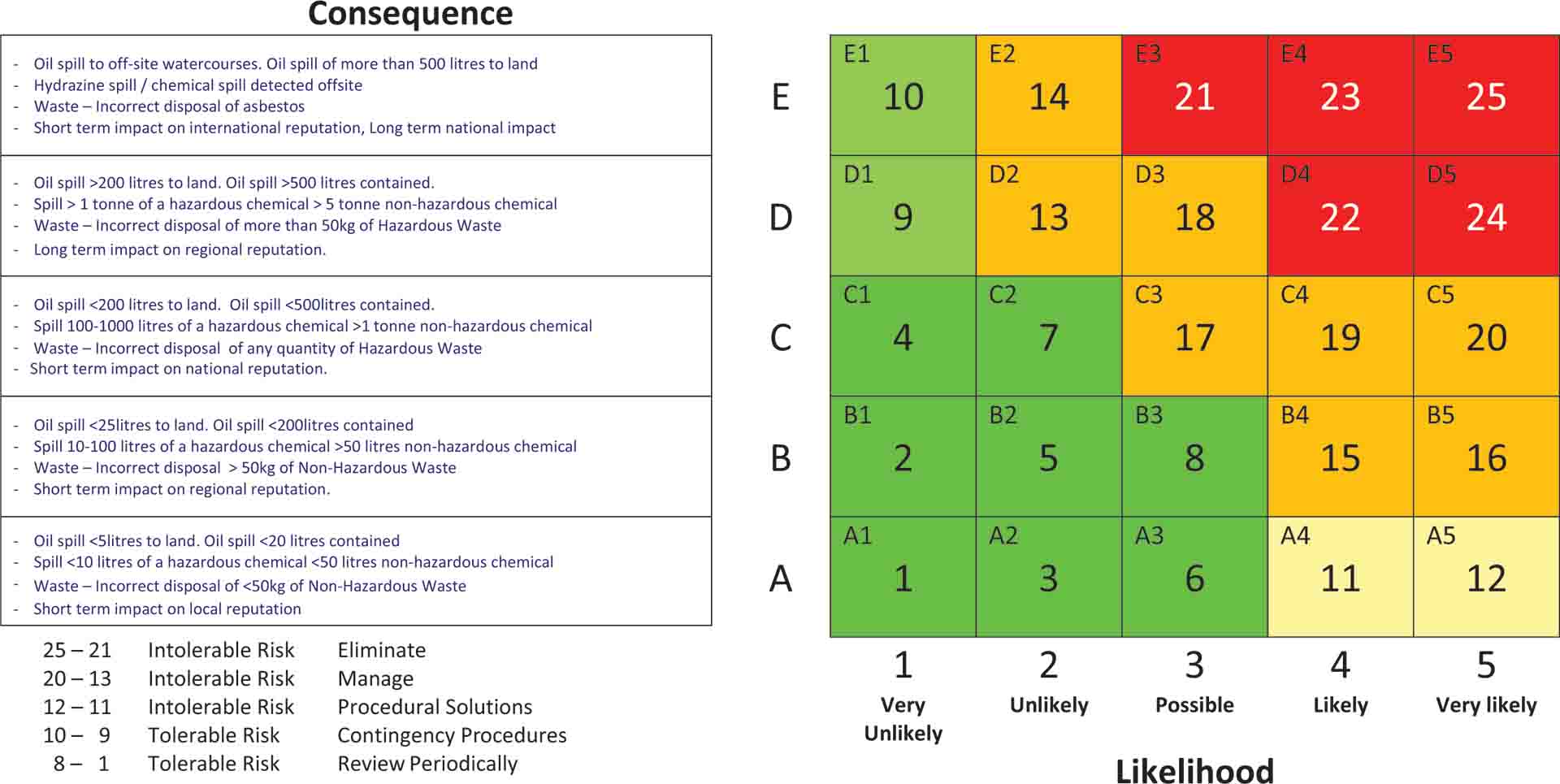
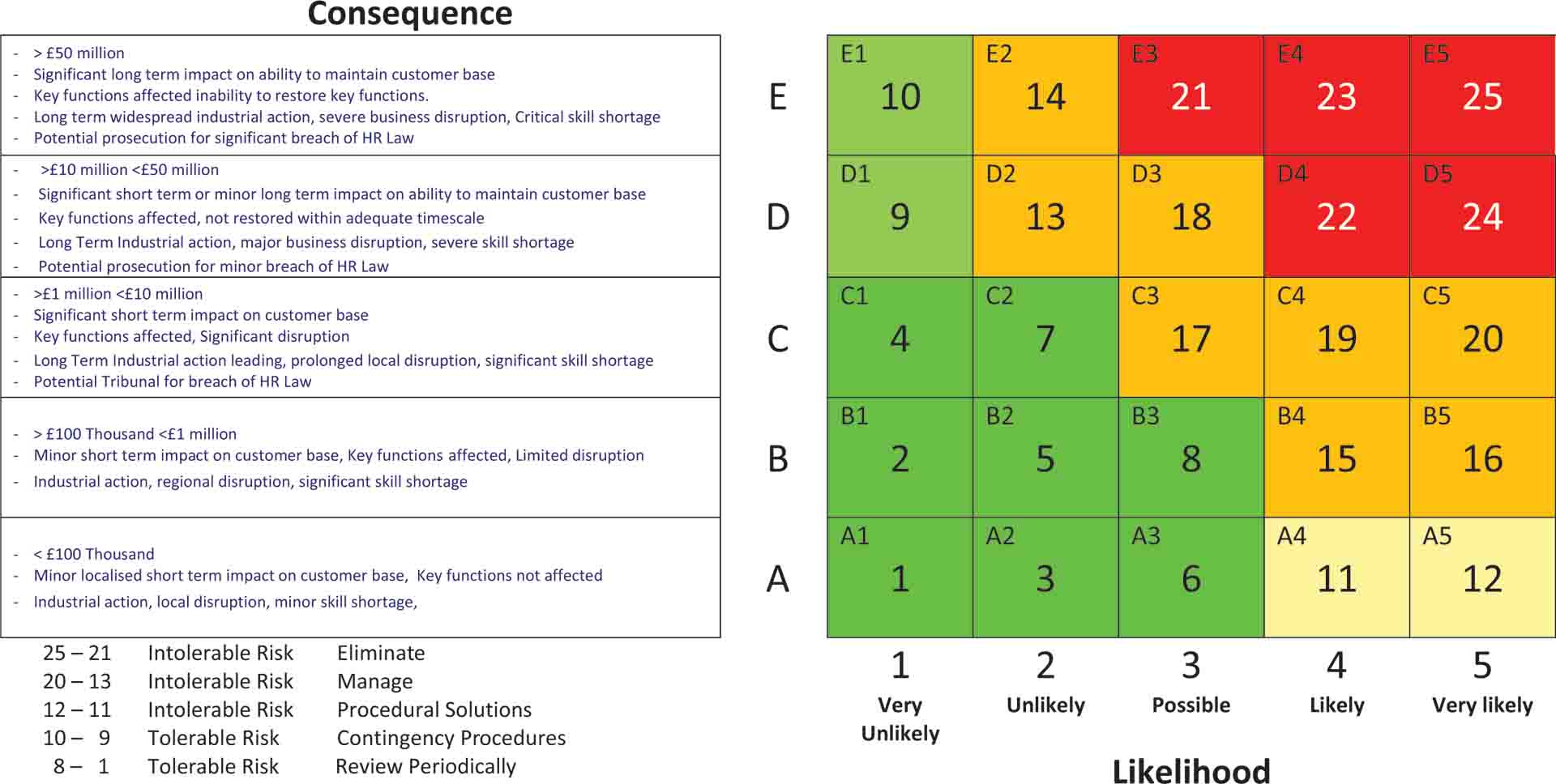
Annex I
Example template: Outline project implementation plan
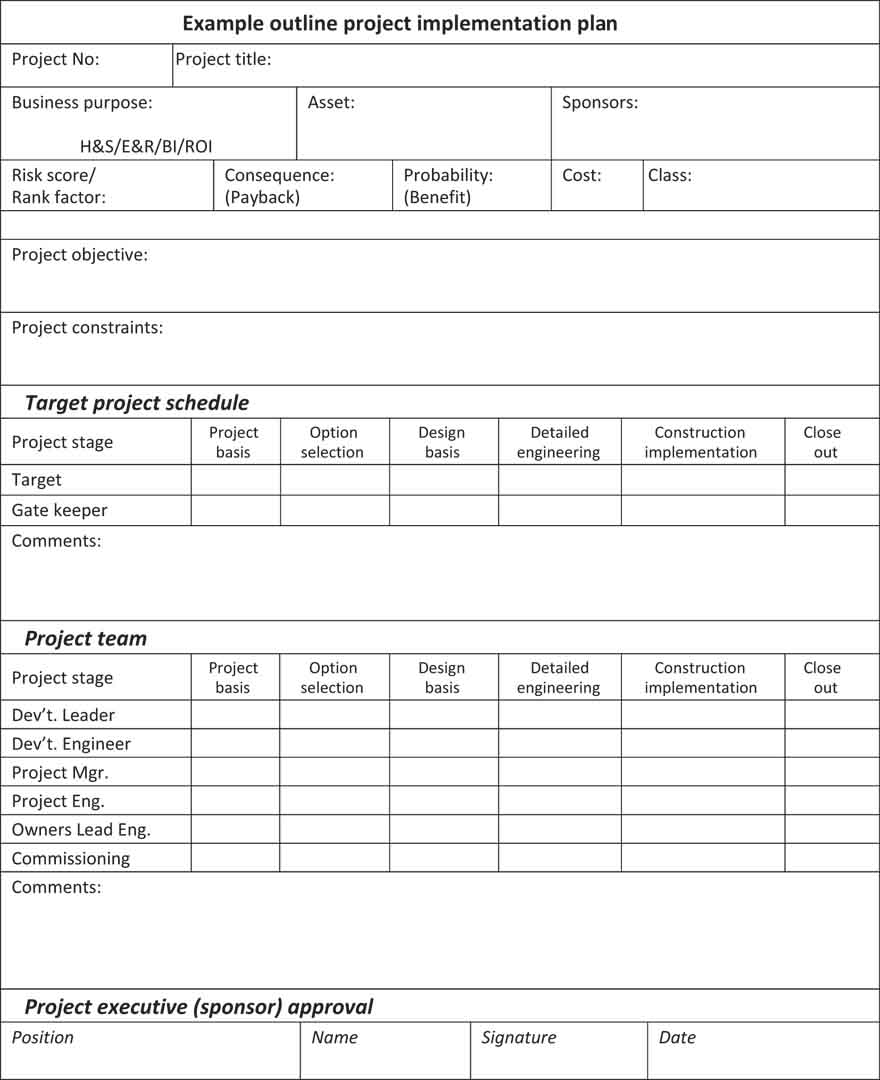
Annex J
Budget development: Developing the portfolio of 'capital' and 'expense' projects
Project ranking and screening
- Resources (finance and experienced people) tend to be limited, therefore best use should be made of the available resources to deliver the maximum benefit to the performance of the business:
- Available resources should be applied to the projects which will give the business the best return.
- Wasted effort on failed projects should be eliminated: these do not make it all the way through the development and implementation process.
- There should be in place a robust ranking and screening process which enables organisations to identify, rank and select, during budget development, those projects which will deliver the required business impact.
- Typically there are only two basic reasons to spend 'capital' or 'expense' funds on a project or initiative:
- The elimination of an unacceptable risk:
- health and safety;
- environmental and reputation, and
- capacity maintenance (i.e. replacement of life expired assets and equipment which pose an unacceptable business interruption risk.)
- Return on investment (ROI): justifiable and affordable investments which will reduce costs or increase income.
- The elimination of an unacceptable risk:
- Although only one of these, ROI, will directly improve profit, the others will reduce the likelihood of unwanted events which may have a dramatic impact upon the overall performance of the business.
Acknowledgements
EI Guidance on meeting expectations of EI Process safety management framework was commissioned by the Energy Institute (EI) Process Safety Committee (PSC) and prepared by Martin Ball (Bossiney Consulting). During this project, PSC members included:
Martin Ball | Bossiney Consulting |
David Bleakley | ConocoPhillips |
John Brazendale | Health and Safety Executive |
John Briggs | Kuwait Petroleum Internationa |
Gus Carroll | Centrica |
Jonathan Carter | Marsh |
James Coull | Total |
Peter Davidson | UKPIA |
Graeme Ellis | ABB |
Dr David Firth | Chilworth Group |
Peter Gedge (Chair) | BP |
John Henderson | CB&I (BCECA) |
Bob Kilford | EDF Energy |
King Lee (Vice-Chair) | Lloyd’s Register |
Paul McCulloch | E.ON |
SreeRaj Nair | Chevron |
Peter O’Toole | Tullow Oil |
John Pond | Consultant |
Dr Niall Ramsden | ENRG Consultants |
Andy Robertson | Nexen |
Toby St.Leger | ConocoPhillips |
Dr Mark Scanlon (Secretary) | Energy Institute |
Don Smith | Eni UK |
The following additional individuals are acknowledged for commenting on the draft for consultation of this series of publications:
Lee Allford | European Process Safety Centre |
John Armstrong | E.ON |
Mike Beanland | ABB |
Amanda Cockton | Health and Safety Executive |
Peter Davidson | UKPIA |
Edwin Ebiegbe | Consultant |
Allen Ormond | ABB |
Technical editing was carried out by Stuart King (EI), and assisted by Sam Daoudi (EI).
Affiliations are correct at the time of contribution.
Our publications website is designed exclusively for EI members and customers to easily access and download PDF versions of our publications. For hard copies, please contact the EI Publishing Team at [email protected]. To access previously downloaded copies go to My publications.
-
User Type
-
PDF Document
-
Hard copy
-
25% discount on most EI publications
-
Free access to other EI publications
- Technical partners
- Free
- Contact us
- Technical company members
- Free
- Contact us
- Limited access
- EI member
- Free
- Contact us
- Non-member
- Free
- Contact us
Your membership
Technical partners
-
PDF Document
Free -
Hard copy
Contact us -
Free access to other EI publications
Your membership
Technical company members
-
PDF Document
Free -
Hard copy
Contact us -
Limited access to other EI publications
Your membership
EI member
-
PDF Document
Free -
Hard copy
Contact us -
Limited access to other EI publications
Your membership
Non-member
-
PDF Document
Free -
Hard copy
Contact us -
Limited access to other EI publications